Titel: | Ueber die Stahlfabrication in Yorkshire nebst einer Vergleichung der vorzüglichsten Stahlhütten Europa's; von Le Play, Berg-Oberingenieur. |
Fundstelle: | Band 91, Jahrgang 1844, Nr. CXIV., S. 444 |
Download: | XML |
CXIV.
Ueber die Stahlfabrication in Yorkshire nebst
einer Vergleichung der vorzuͤglichsten Stahlhuͤtten Europa's; von
Le Play,
Berg-Oberingenieur.
Aus den Annales des Mines, Tom. III. 3. Lief. 1843. durch Heßler's Jahrbuch fuͤr
Technik, Physik und Chemie Jan. 1844 S. 53.
Mit Abbildungen auf Tab.
VI.
Ueber Stahlfabrication in Yorkshire.
Die europäischen Stahlhütten zerfallen in zwei Hauptclassen, welche in Bezug auf die
Wichtigkeit der Production beinahe auf der nämlichen Stufe stehen, sich aber, was
die technischen und ökonomischen Bedingungen anbelangt, wesentlich von einander
unterscheiden. Die Hütten, welche Roh- oder Schmelzstahl erzeugen, beobachten
Verfahrungsarten, welche jenen, die auf dem Continent bei Fabrication des
Schmiedeisens im allgemeinen befolgt werden, ziemlich analog sind. Die Eisenerze,
welche in diesen Hütten verarbeitet werden, müssen mehrere besondere Eigenschaften
besizen, welche im höchsten Grade nur im Spatheisenstein sich vereinigt finden:
deßwegen finden sich die Hauptmittelpunkte der Rohstahlfabrication in der Nähe des
Vorkommens von Spatheisensteinen, und da diese Erze, so wie die verschiedenen
Producte, welche der Darstellung des Rohstahles vorausgehen, ausschließlich nur mit
vegetabilischem Brennstoff verarbeitet werden können, so ist die Stahlproduction in
den Hütten dieser ersten Kathegorie in jeder Gegend immer auch durch die
Brennstoffmenge beschränkt, welche die in der Nachbarschaft befindlichen Forste
liefern. In solcher Lage befinden sich vier Hauptgruppen von Stahlhütten, welche dem
Handel beiläufig zwei Drittel des auf dem Continente fabricirten Rohstahls liefern.
Die erste Gruppe bilden die zahlreichen, in Steiermark und Kärnthen um die
unerschöpflichen Lager von Eisenerz und Hüttenberg herumliegenden Hütten; die zweite
Gruppe ist die Rheingruppe, am Sieg, an der Mosel, an der Saar u. s. w. in der Nähe
des durch den Namen Stahlberg charakterisirten Lagers
gelegen. Die dritte Gruppe ist jene der Jser, die ihre Erze aus den Lagern von
Alleward und Saint-George d'Heurtières erhält, und die vierte Gruppe endlich
ist die Thüringer Gruppe, deren Hauptlager auch den Namen Stahlberg führt, und deren
Hütten alle in dem an Holz und Wasserkraft reichen Thüringerwald liegen.
Die Stahlhütten der zweiten Classe erzeugen Cementstahl, für welchen Schmiedeisen das
Hauptmaterial ist. Die Erzlager, welche zur Umwandlung in Cementstahl geeignetes
Schmiedeisen liefern, sind viel zahlreicher als die Erzlager für Rohstahl; man kann
die Zahl dieser Lager als unbegränzt betrachten. Dessen ungeachtet findet man, wenn
man bis auf den Ursprung des Eisens, welches in den Hauptgruppen der
Cementstahlhütten verarbeitet wird, zurükgeht, daß es noch ein beinahe
ausschließendes Privilegium einer geringen Zahl von Lagern der scandinavischen
Kette, des Urals und der Pyrenäen ist, den Stahlhütten, und nur gewissen
Stahlhütten, das Material zu liefern, welches sie ausschließlich mit Holzkohle
verarbeiten.
Da das Cementiren keinen Abgang an Grundmaterial bewirkt, so ist es nicht nöthig, daß
der Cementstahl so wie der Rohstahl in der Nähe der Erzlager erzeugt werde. Das
Schmiedeisen, welches sich vorzugsweise zur Cementstahlfabrication eignet, wird viel
theurer verkauft als die andern Eisensorten. Die Hütten, welche solches Eisen
erzeugen können, suchen daher die Production so weit zu steigern, als es die
Holzmittel der Gegend erlauben und es bleibt im allgemeinen kein Brennmaterial für
die Umwandlung des Eisens in Stahl mehr übrig. Das eigentliche Cementiren erfordert
zwar nur sehr wenig Brennmaterial; sehr beträchtlich ist aber der Brennstoffbedarf
bei den für die Stahlindustrie weit wichtigern und wesentlichen Arbeiten, durch
welche die rohen cementirten Stäbe in Handelsproducte umgewandelt werden. Noch zwei
andere wichtige Umstände erklären das Entferntliegen der Cementstahlhütten von der
Gegend, wo das in Stahl umzuwandelnde Eisen erzeugt wird. Es wird in dieser
Abhandlung dargethan werden, daß die mineralischen Brennstoffe bei gleicher
Heizkraft in der Cementstahlfabrication den vegetabilischen Brennstoffen entschieden
vorgezogen werden müssen. Würden die großen Eisenhämmer des Urals und Schwedens auch
über einen
unbeschränkten Brennstoffvorrath disponiren können, so würden sie sich in der
Verwandlung ihres eigenen Eisenerzeugnisses in Cementstahl doch nicht in so
günstigen Verhältnissen befinden, wie die auf den Steinkohlenbeken des westlichen
Europa befindlichen Hütten.
Die für die Cementstahlfabrication günstigsten Gegenden sind jene, welche durch
wohlfeile Communicationsmittel das Eisen aus Schweden oder Rußland beziehen können,
die reichlich mit mineralischem Brennstoff versehen sind, deren Akerbauverhältnisse
die Ansammlung einer bedeutenden Population von Arbeitern gestatten, die den Stahl
an Ort und Stelle zu den verschiedenen Geräthen, als Sensen, Sicheln, Feilen,
Raspeln, Sägeblättern und andern Schneidewerkzeugen u. s. w. verarbeiten und welche
ihren Producten einen großen Markt eröffnen können.
Der Theil von Yorkshire (Sheffield, Attercliffe, Morsborough u. s. w.), in welchem
die meisten Stahlhütten Großbritanniens concentrirt sind, vereinigt alle diese
Bedingungen im höchsten Grade in sich und steht hierin allen Theilen Großbritanniens
voran. Es fabricirt jezt Yorkshire 18mal mehr Stahl als das ganze übrige England
zusammen.
Verfahren bei der Cementstahlfabrication in Yorkshire. Der
Cementirofen hat seit anderthalbhundert Jahren in Gestalt und Dimensionen große
Modificationen erlitten; man hat die alten Oefen, in welchen auf einmal wenigstens
5000 Kil. (8930 Wiener Pfd.) Eisen behandelt wurden, nach und nach immer vergrößert
und in der lezteren Zeit hat man Oefen gebaut, welche bis 40,000 Kilogr. (71,440
Pfd.) Eisen aufnehmen können. Es scheinen hiebei aber die in Beziehung auf Oekonomie
und Bequemlichkeit der Arbeit entsprechendsten Gränzen überschritten worden zu seyn.
Viele Oefen nehmen nur 10,000–12,000 Kil. (17,860–21,432 Pfd.) auf,
und am liebsten baut man die Oefen, selbst in Hütten, wo es durchaus nicht an Arbeit
fehlt, für 15,000–20,000 Kilogr. (26,790 bis 35,720 Pfd.). Alle Oefen
bestehen aus zwei gleichen parallelopipedischen Cementirkästen, die durch den
Heiz- oder Feuerraum getrennt sind und beinahe an der ganzen Oberfläche von
den erhizten Gasen umzogen werden, welche nach langsamer Umkreisung der Kästen das
Ofengewölbe durch die am Anfange desselben angebrachten Oeffnungen verlassen.
Cementirofen. — Die Fig. 1–8 zeigen die in
Yorkshire gebräuchlichste Einrichtung des Cementirofens, worin auf einmal 17,600
Kilogr. (31,433 Pfd.) cementirt werden, welcher alle Bedingungen zu einer guten
Cementation erfüllt und sich durch sehr geringen Brennstoffbedarf auszeichnet. Die Kästen sind
entweder aus feuerfesten Ziegeln oder aus sorgfältig zugehauenem quarzreichem
Sandstein gebaut, wozu die Materialien sich in Yorkshire im Ueberfluß finden. Die
verticalen Wände aus Sandstein sind gewöhnlich 0,153 Met. (5⅔ Wien. Zoll)
dik, und jene aus Ziegelsteinen sind aus zwei Reihen auf die schmale Seite
gestellter Ziegeln zusammengesezt und haben in ihrer ganzen Dike nur 4″
3″′. Die horizontale Mauer, welche den Boden der Kästen bildet, ist
gewöhnlich um die Hälfte diker als die verticalen Wände. Bei den Kästen und Ziegeln
ist sie aus drei Lagen auf die breite Fläche gelegter Ziegeln gebildet und die
Bindung ist durch eine dünne Schichte feuerfesten Thons hergestellt.
Indem ich die Cementirkästen von Oefen sehr verschiedener Dimensionen verglich,
zeigte sich, daß sich diese Dimensionen nach einem einfachen Gesez aus der bei jeder
Operation verarbeiteten Eisenmenge ergeben. Ferner habe ich constatirt, daß
erfahrene und gewandte Arbeiter, ohne den Erfolg der Operation aufs Spiel zu sezen,
das Volumen des in jeden Kasten eingetragenen Eisens bis auf 36/100 des ganzen
Kastenvolums treiben können. Die längste Dimension des inneren leeren Raumes der
Kästen (ich will sie die Länge heißen) ist immer horizontal und ihr Kubus ändert
sich in gleichem Verhältniß mit dem Gewichte der Beschikung (des Einsazes) oder mit
dem Volum des Kastens, so daß die für 10,000 Kilogr. (17,860 Pfd.) Beschikung
gewöhnliche Länge von 2,8 Met. (8,84 Wien. Fuß) für eine Beschikung von 17,600
Kilogr. (31,433 Pfd.) auf 3,353 Met. (10,59 Fuß) steigt. Man entfernt sich zwar
manchmal etwas von dem Geseze, und das geschieht in dem Falle, wo die zu
cementirenden Stangen eine bestimmte Länge haben sollen. Die Dike des Kastens (so
heiße ich die geringste Dimension des innern Kastenraumes) ist bald vertical, bald
horizontal, varirt aber unter allen Dimensionen am wenigsten; sie bleibt gewöhnlich
zwischen 0,70 und 0,90 Met. (26″ 3″′ und 33″
8″′). Bei Oefen, wo die Beschikung 24,000 Kilogr. (42,864 Pfd.) nicht
überschreitet, ändert sich diese Dimension noch etwas, wie die Kubikwurzel aus der
Beschikung, und über diese Gränze hinaus wächst sie in einem etwas geringern
Verhältniß. Ueberhaupt hat auch die vorerwähnte Vergleichung einer großen Zahl von
Cementiröfen zu folgenden empirischen Formeln geführt, nach welchen man sehr
annäherungsweise die Dimensionen der Cementirkästen für Oefen bestimmen kann, in
welchen die Beschikung zwischen 10,000 und 24,000 Kilogr. wechselt. In diesen
Formeln bedeutet P die ganze Beschikung in Kilogrammen
und v, l, e, stellen das innere Volum, die Länge und
Dike der Kästen vor: v = 0,000178 Kubikmet. × P; l = 0,13 Met. ×
P; e = 0,032
Met. × P1 Meter betraͤgt 3,16 Wien. Fuß..
Für den dargestellten Ofen ist: v = 3,138 Kubikmeter; l = 3,41 Meter; e = 0,86
Meter, und bei einem Ofen für 10,000 Kilogr. Beschikung ist v = 1,764 Kubikmet.; l = 2,80 Met.; e = 0,70 Meter.
Cementirkästen.— Auf die sechs rechtekigen
Außenflächen jedes Kastens wirken, mit Ausnahme der Stüzungspunkte, die vorzüglich
an der untern Fläche unerläßlich sind, die Flammen ein. Diese leztere Fläche ruht
auf massiv gemauerten, im Durchschnitt vierekigen Pfeilern, welche zwischen sich
leere, auf der Länge der Kästen perpendiculäre Räume der nämlichen Gestalt
lassen.
In dem dargestellten Ofen, dessen Cementirkästen aus quarzreichem Sandstein gebaut
sind, haben die massiven Pfeiler oder Stüzen und die Canäle zwischen denselben 0,229
Meter (8,6 Zoll) Seite. Die verticalen Wände der Kästen sind durch sechs kleine
Zwischenwände gestüzt, Fig. 1, welche 0,114 Met.
(4,3 Zoll) dik und zwischen den Kästenwänden und der äußern Ofenmauer nach der
ganzen Höhe der Kästen emporgeführt sind. Sieben andere Scheidewände Fig. 1, 2 und 3 sind zwischen den zwei
Kästen über dem Heizraume angebracht, und manchmal geht die mittlere Scheidewand,
welche diker ist als die andern, bis unter das Niveau des Rostes hinab und theilt
den Heizraum in zwei Abtheilungen. Bei den aus Baksteinen gebauten Oefen haben die
massiven Pfeiler oder Stüzen und die Canäle unterhalb den Kästen gewöhnlich 0,114
Meter (4,2 Zoll) Breite oder die mittlere Ziegeldimension. Die Stüzungen oder
Streben sind aus zusammengefügten, mit der schmalen Seite in die äußere Ofenmauer
eingesezten Ziegeln gebildet; sie sind rautenförmig angeordnet und in der nämlichen
Horizontallinie durch zwei Ziegellängen abgesondert.
Heizraum. — Die zwei Cementirkästen stehen in dem
nämlichen Niveau und symmetrisch gegen den sie trennenden Heizraum, der immer eben
so lang ist wie die Kästen. Die Breite c dieses
Heizraums oder der Zwischenräume zwischen zwei Kästen varirt mit dem Gewicht der
Beschikung (des Einsazes) nahe nach der Formel c =
0,0176 Met. × P, die aber nur in den
Fällen genaue Resultate gibt, wo der Einsaz zwischen 13,000 und 24,000 Kilogr.
(23,218–42,864 Pfd.) beträgt. Für Oefen von größeren Dimensionen ist der Coefficient kleiner und
für kleinere Oefen wächst er. Für den dargestellten Ofen gibt die Formel und die
Beobachtung für den Heizraum die Breite von 0,458 Met. (17,2 Zoll). Die fünf
Schmiedeisenstangen haben bei 0,033 Met. (14½ Linien) im Gevierte; sie werden
von fünf gußeisernen Querstangen oberhalb des Aschenfalls getragen, der dieselbe
Breite wie der Heizraum hat und etwa 0,73 Met. (27,5 Zoll) lang ist. Die obere
Fläche der Stangen liegt 0,381 Met. (13,3 Zoll) tiefer als der Untertheil der unter
den Kästen angebrachten Canäle. An den zwei entgegengesezten Ofenwänden sind nach
der Achse des Heizraumes zwei 0,458 Met. (17,2 Zoll) breite und 0,305 Met. (11,4
Zoll) hohe Oeffnungen angebracht, deren Schwelle 0,305 Met. (11,4 Zoll) über den
Roststangen liegt. Diese Oeffnungen dienen zum Aufgeben der Steinkohlen auf den Rost
und sind während der Arbeit durch gußeiserne Thüren verschlossen.
Die Umhüllung (äußere Ofenmauer), welche die Kästen und den Heizraum einschließt, ist
aus vier verticalen Mauern gebildet, welche von zwei gedrükten und in einem
Klosterbogen vereinigten Gewölben bedekt sind. Die Gestalt und Dimensionen dieser
Umhüllung hängen innig mit den Dimensionen der Kästen und des Herdes zusammen. Die
verticalen Wände stehen von den äußern Flächen der Kästen 6 Zoll ab und die Gewölbe
nehmen genau im Niveau der obern Fläche der Kästen ihren Anfang; ihre Höhe wechselt
von 0,86–1,01 Meter (2 Fuß 8 Zoll bis 3,19 Fuß). Bei dem abgebildeten Ofen
beträgt sie 0,91 Met. (2 Fuß 10 Zoll). Diese Höhe ist nöthig, damit die Arbeiter,
wenn sie die Kästen beschiken oder den Stahl herausnehmen, im Ofen bequem
manipuliren können. Der innere leere Raum des Ofens ist demnach rechtekig und mißt
an der dem Heizraume parallelen Seite 4,01 Met. (12,77 Fuß) und an der gegen den
Heizraum senkrechten Seite 3,5 Met. (11 Fuß). Am Anfange der Gewölbe sind immer
sechs Oeffnungen angebracht und zwar zu drei auf den zwei entgegengesezten Seiten
des Ofens Fig.
3. Durch die zwei größten, in der Achse des Ofens und über den
Eintragthüren angebrachten, begeben sich die Arbeiter in den Ofen, und die vier
kleineren, welche symmetrisch vor den kleinen Außenseiten der Kästen angebracht
sind, dienen zum Eintragen der Eisen- und zum Herausnehmen der Stahlstangen.
Alle diese Oeffnungen sind während des Cementirprocesses durch Wände aus Ziegeln und
Lehm hermetisch verschlossen. Zwei noch kleinere vierekige Oeffnungen Fig. 5 von
wenigstens 0,114 Meter (4,3 Zoll) Seite sind an beiden Seiten des Ofens etwa in der
Mitte der Höhe der Cementirkästen angebracht; sie sind die Enden (Ausmündungen)
kleiner Canäle, durch
welche der Arbeiter während des Ganges der Operation zu verschiedenen auf einander
folgenden Zeitpunkten aus den Cementirkästen Probestäbe ziehen kann, die gleich beim
Beschiken der Kästen eigens zu diesem Ende mit eingesezt wurden. Nach diesen Stäben
beurtheilt man das Fortschreiten des Cementirens und erkennt den Moment, wo dasselbe
beendigt ist. Nachdem die Flamme die Cementirkästen umzogen hat, tritt sie aus dem
Heizraum durch acht Oeffnungen Fig. 1, 2 und 3 aus, wovon jede der vier
verticalen Wände dieses Heizraumes zwei enthält. Diese Oeffnungen, welche die Flamme
gleichmäßig vertheilen, sind in gleichem Niveau mit der oberen Fläche der Kästen, am
Anfange des Gewölbes angebracht, sind vierekig von 0,153 Meter (5⅔ Zoll)
Seite und stehen durch Canäle von dem nämlichen Durchschnitt mit sechs verticalen
vierekigen Schornsteinen (von 0,204 Meter oder 7½ Zoll) Seite in Verbindung,
die sich bis auf einige Zolle unter dem Niveau des Gewölbes erheben.
Ein großer Thurm, Fig. 1, 2, 3 und 4, auf festem Fundamente stehend, und aus gewöhnlichen Ziegeln gebaut,
führt die aus den kleinen Schornsteinen hervorkommenden Gase in die äußere Luft. Er
hat eine beinahe conische Gestalt und sein horizontaler Durchschnitt ist kreisrund.
Seine Hauptdimensionen, die in jeder Hütte anders sind, waren bei dem dargestellten
Ofen folgende: äußerer Durchmesser am Boden 8,08 Meter (25,83 Fuß); Mauerdike am
Boden 0,53 Meter (19¾ Zoll); innerer Durchmesser der oberen cylindrischen
Ausmündung 0,52 Meter (19,5 Zoll); Mauerdike daselbst 0,11 Meter (4,1 Zoll);
Erhöhung des conischen Theiles über den Aschenfall 11,05 Meter (34,91 Fuß); Höhe des
cylindrischen Theils 1,22 Meter (3,85 Fuß); Höhe des ganzen Thurmes 12,27 Meter
(38,76 Fuß).
Der Durchmesser des Thurmes unten am Boden ist immer durch die Bedingung bestimmt,
daß der Thurm den Ofen und dessen Schornsteine einschließen muß. Der Raum zwischen
dem Ofen und dem Thurm ist bis zur Höhe, wo das Gewölbe anfängt, mit gewöhnlichem
Mauerwerk ausgefüllt, Fig. 1, 2 und 3. An entgegengesezten
Seiten führen nach der Richtung der Achse des Heizraumes durch den Thurm zwei 1,83
Meter (5,78 Fuß) breite Gänge, Fig. 1, 2 und 4, die unten im Niveau des
Aschenfalls ihren Anfang nehmen und 1,52 Meter (4,8 Fuß) über den Boden hinaus sich
erheben; ihre ganze Höhe beträgt 3,43 Meter (10,77 Fuß).
Die Cementiröfen stehen theils isolirt, theils sind ihrer 2 bis 5 in einer einzigen
Hütte vereinigt. Gewöhnlich enthält eine Hütte zwei Oefen, und die dargestellte gehört unter jenen, die
ich gesehen habe, zu den am besten eingerichteten.
Die zwei Oefen sind in einer und der nämlichen rechtekigen 32,62 Meter (73,07 Fuß)
langen und 10,52 Meter (33,24 Fuß) breiten Halle Fig. 6, 7 und 8 vereinigt. Vor den
Heizthüren und nach der Richtung der großen Achse der Halle sind Gräben angebracht,
welche die nämliche Breite haben, wie die durch den Thurm zum Ofen führenden Gänge,
und sich in das Atelier hinein 1,22 Meter (3,85 Fuß) über die Grundmauer dieses
lezteren hinaus erstreken. Man läßt zwischen den Mauern der Halle, zwischen den
Grundmauern des Thurmes und den Gräben, Durchgänge von 3,85 Fuß.
Die Halle oder Hütte ist innerlich so hoch, daß die Arbeiter leicht manipuliren und
die zur Umwandlung in Stahl bestimmten Eisenstangen aufrecht an die Wand stellen
können. Ein großes Thor gestattet den Wägen in die Mitte der Halle zu fahren, um das
sonst nöthige Uebertragen der Stangen, von den Wägen in die Halle hinein und aus der
Halle zu den Wägen hinaus, zu ersparen. Man muß deßwegen zwischen den Oefen einen
beträchtlichen Raum belassen, der übrigens auch noch nöthig ist, um die
Eisen- und Stahlstangen zu wägen, die Eisenstangen zu gehöriger Länge
zuhauen, die für jede Post erforderliche Quantität Steinkohlen deponiren und endlich
um alle beim Cementirproceß selbst nöthigen Manipulationen bequem ausführen zu
können.
In der Umgebung von Liverpool und Bristol fand ich nach einem ganz andern Principe
construirte Cementiröfen. Die Cementirkästen, der Heizraum, die Canäle und die
äußere Ofenmauer sind genau wie bei den Oefen in Yorkshire angeordnet; der
Unterschied liegt vorzüglich darin, daß das die äußere Ofenmauer bedekende Gewölbe
beweglich ist und daß der Luftzug durch eine Esse erzeugt wird. Das Gewölbe bildet
immer einen Klosterbogen, ist aber viel gedrükter wie bei den Oefen, von denen
vorher die Rede war; dessen Höhe varirt kaum zwischen 0,40 und 055 Meter (15 und 20
Zoll). Die Baksteine, aus welchen dieses Gewölbe gebildet ist, ruhen auf einem
vierekigen gußeisernen Rahmen, der selbst wieder von vier kleinen Rädern getragen
wird, die nach Bedarf auf parallelen Eisenschienen hinbewegt werden können, so daß
man um die Kästen zu entleeren, das Gewölbe leicht zur Seite schieben kann. Bevor im
Ofen Feuer gegeben wird, bringt man das Gewölbe wieder über denselben und lutirt den
Raum zwischen dem fixen und beweglichen Theil mit Lehm.
Die Esse hat immer ihr eigenes, von jenem der Oefen unabhängiges Fundament und die Oefen,
gewöhnlich zwei an der Zahl, sind symmetrisch zu beiden Seiten dieser Esse
angeordnet. Die durch die Verbrennung erzeugten Gase treten durch eine im Centrum
des Obertheils des beweglichen Gewölbes angebrachte Oeffnung aus und gelangen durch
einen horizontalen fixen Fuchs (Canal), der oberhalb des Ofens an eisernen, am
Dachstuhl der Hütte befestigten Stangen hängt, in die Esse. Bei dieser Einrichtung
suchen die Verbrennungsgase unmittelbar aus dem Herd in den Fuchs zu treten, ohne
die Kästen zu umziehen und am Umfange zu erhizen. Dem wird dadurch begegnet, daß der
Zwischenraum zwischen den Kästen über dem Heizraume durch eine horizontale, im
Niveau des obern Randes der Kästen angebrachte Scheidewand abgesperrt ist, so daß
die Flamme gezwungen ist, in dem 0,153 Meter (5⅔ Zoll) breiten Raum zwischen
den Kästen und der äußeren Ofenmauer zu circuliren; ferner verzögert man den
Austritt der Flamme auch durch Verminderung der Weite der im Niveau des obern Randes
der Kästen befindlichen Canäle um etwa 0,038 Meter (1½ Zoll). Die Esse
erzeugt im Ofen immer, ausgenommen beim Anheizen, einen überschüssigen Zug: man
regulirt den Zug nicht, wie bei den Oefen in Yorkshire, durch Einwirkung auf den
Rost, sondern durch Aufmachen einer Oeffnung am horizontalen Fuchs, welche einer um
so größern Menge Luft den Eintritt gestattet, je mehr man den Vortheil der
Lebhaftigkeit des Verbrennens beschränken will.
Diese Bauart scheint mir in mehrfacher Beziehung vortheilhaft: sie gestattet ein
leichtes Beschiken und Entleeren der Kästen und eine leichte Führung des Feuers;
obgleich sie viel Guß- und Schmiedeisen zu Armirungs- und
Befestigungstheilen fordert, was beim andern System nicht nöthig ist, so kommt die
erste Anlage doch nicht so beträchtlich theurer, wie es den Anschein hat. Der
Brennstoffbedarf ist etwas geringer, vorausgesezt daß die Arbeiter bei Regulirung
des Feuers und beim Aufgeben des Brennstoffes auf den Rost die gehörige
Aufmerksamkeit verwenden. Ich halte überhaupt dafür, daß man überall einem solchen
Ofen den Vorzug vor den Oefen in Yorkshire geben müsse, wo die Handarbeit wohlfeil
und wo nur mit kleinen Eiseneinsäzen gearbeitet wird. In einer Cementstahlhütte
müssen überdieß noch vorhanden seyn: ein Amboß, Kaltmeißel und Hämmer, um die
Eisenstangen zuhauen zu können; Waagen zum Wägen des Eisens und Stahles;
Schiebkarren zum Zuführen der Kohlen aus dem Hof zum Ofen; Schaufeln, Schürstangen,
gerade und krumme, zur Versorgung und Reinigung des Rostes.
Hauptmaterialien und Brennstoff. — Von der guten
Wahl dieser Materialien hängt vorzüglich der gute Erfolg bei der Cementstahlfabrication ab. Auch
die vervollkommnetste Manipulation könnte das nicht ersezen, was dem Eisen an
Qualität abginge.
In dieser Beziehung dienen den Arbeitern unzählige, seit 200 Jahren gesammelte
Erfahrungen zur Richtschnur, und man kennt seit langer Zeit genau die Qualitäten der
verschiedenen in Yorkshire angewendeten Eisensorten. Dennoch gelang es bis auf den
heutigen Tag nicht, diese Kenntnisse, welche den Arbeitern täglich bei Ausübung
ihrer Kunst wohl zu statten kommen, und welche allein die Grundlage zu einer
vollständigen Theorie der Stahlfabrication bilden können, in das Gebiet der
Wissenschaft einzureihen. Unter den Hindernissen, welche die Gelehrten bei ihren
Studien dieser Art zu überwinden haben, gehört vorzüglich der Umstand, daß die
Künstler und Arbeiter aller Arten im allgemeinen so schwer zur Mittheilung ihrer
Erfahrungen zu bewegen sind, und daß es namentlich bei den Industriellen in
Yorkshire zum System geworden, keine solchen Mittheilungen zu machen. Diejenigen,
welche den commerciellen Theil der Stahlfabrication dirigiren, sind zwar liberaler;
ihnen fehlt aber wieder die technische Richtung des einfachen Arbeiters, welche, um
Aufschluß über die Operationen geben zu können, unentbehrlich ist. Ferner ist es für
den Gelehrten sehr schwer, sich in die Sprache der Arbeiter zu finden, z. B. in
manchen Fällen herauszubringen, was der Arbeiter mit dem Ausdruk gesundes, starkes,
hartes Eisen u. s. w. für Qualitäten bezeichnen will. Und was diese leztere
Schwierigkeit noch sehr erhöht, ist der Umstand, daß die nämlichen Ausdrüke bei
zwei, bei verschiedenen Zweigen der Stahlfabrication beschäftigten Arbeiten nicht
immer die gleiche Bedeutung haben. Endlich muß man sich, um zu Resultaten zu
gelangen die Zutrauen verdienen, gegen die ungenauen Beobachtungen der Arbeiter und
gegen die gewöhnlich übertriebene Schäzung der Wichtigkeit gewisser Eigenschaften
der Materialien gehörig zu schüzen wissen.
Uebrigens sind die Fragen, die Wahl des zu verarbeitenden Eisens betreffend, so
äußerst zusammengesezt, daß ihre ausführliche Lösung ein Buch füllen würde; ich kann
mich daher hier nur auf die Mittheilung der Hauptthatsachen beschränken, welche
durch lange fortgeführte Untersuchungen und in Folge verschiedener günstiger
Umstände bereits constatirt sind.
Eigenschaften des Eisens. — Alles Eisen des
Nordens, welches von den Stahlfabrikanten gesucht wird, zeichnet sich durch eine
körnige (grenue), dichte Structur und durch eine
glänzende bläulich grüne Farbe, die etwas an jene des Zinkes erinnert, aus. Ziemlich
oft findet man im Querdurchschnitt einer Stange diesen Typus in allen Uebergängen
vor einer deutlich ausgesprochenen blättrigen (lamellaire)
und seltener vor einer faserigen (fibreuse) Structur
vorherrschend. Im lezteren Fall ist der Bruch der in der Kälte angehauenen Stangen
kein nahe ebener, sondern sie reißen in Fibern auseinander, die aus einer Menge
neben einander liegenden Blätter zusammengesezt erscheinen. Diese Blätter sind an
der Oberfläche matt weiß, etwas silberartig, und ihr in Folge des in der Kälte
bewirkten Zerbrechens verdrehter Schnitt zeigt einen seidenartigen Reflex nach Art
desjenigen, welchen unter gleichen Umständen raffinirtes Kupfer zeigt. Es ist sehr
schwer, die Stangen kalt zu zerbrechen, selbst dann, wenn sie mit dem Stahlmeißel
stark angehauen sind. Die wesentliche Eigenthümlichkeit dieser Eisengattung ist, daß
sie bei gehöriger Behandlung ein Product gibt, das im höchsten Grade die guten
Eigenschaften des Stahles besizt, d. h. durch Härten eine sehr große Härte und durch
Poliren einen sehr lebhaften Glanz erhält, sich leicht schweißen läßt, einen hohen
Grad von Elasticität besizt und oft ins Feuer gebracht werden kann, ohne daß sie
wieder zu gewöhnlichem Schmiedeisen wird. Alle diese Eigenschaften scheinen im
innigen Zusammenhang mit der Beschaffenheit der Erze zu stehen, von welchen das
Eisen herkömmt: denn als ich dem Ursprung der Eisengattungen, die ich als vorzüglich
gesucht bezeichnete, nachforschte, zeigte es sich, daß sie alle von einer sehr
beschränkten Zahl von Magneteisensteinlagern herkommen. Die Güte und Qualität des
aus dem Eisen erzielbaren Fabrikates bestimmt dessen Rang und zum Theil dessen
commerciellen Werth. Man begreift, daß dieß so seyn müsse, weil die
Fabricationskosten bei jeder Beschaffenheit des Eisens die nämlichen bleiben, und
der Verkaufspreis der Fabricate mit der Vorzüglichkeit des sie liefernden Materials
wächst. Eine zweite sehr wichtige Eigenthümlichkeit des Eisens ist Continuität aller
Elemente der Masse. Mängel in dieser Beziehung äußern sich während der
aufeinanderfolgenden Operationen der Stahlbereitung mehr oder weniger schnell, je
nach der Qualität des Eisens und der Beschaffenheit der besagten Operationen. Das
allgemeinste und entscheidenste Anzeichen liefert das Aussehen der rohen Stangen,
nachdem sie der Cementation unterworfen wurden. Diese Stangen müssen ihre
ursprüngliche Form behalten; ihre Oberfläche kann mit einer großen Zahl kleiner
Bukeln bedekt seyn, welche von einem Gase erzeugt zu werden scheinen, welches in der
Eisenmasse frei wird, sobald diese im Ofen einen gewissen Grad von Weichheit
angenommen hat; es ist aber wesentlich, daß diese Art von Blattern oder Blasen sehr
klein (kleiner als 1 Centimeter oder 4,5 Linien) und daß sie beinahe gleichmäßig
über der ganzen Oberfläche der Stangen vertheilt sind. Große Blasen und vorzüglich
große, auf der Stange unregelmäßig zerstreute Spalten und Sprünge sind eines der sichersten
Anzeichen von Mangel an Continuität. Die Fabrikanten pflegen diese Mangelhaftigkeit
mit der Redensart, das Eisen hat keine Körper oder ist nicht gesund u. s. w., zu
bezeichnen.
Diese Eigenthümlichkeit ist nicht etwa unabhängig von der Beschaffenheit der
Eisenerze: denn sie entwikelt sich bei aus verschiedenen Erzen dargestelltem Eisen,
wenn dieses auch auf ganz gleiche Art behandelt wird, in verschiedenem Grade. Es ist
jedoch leicht zu erweisen, daß auch die geringsten Nüancirungen und Modificationen
in der metallurgischen Behandlung derselben Erze zur Hervorrufung deutlich
ausgesprochener Verschiedenheiten in der Qualität des Eisens hinreichen. Die
außerordentliche Verschiedenheit des Preises, die zwischen den besten Fabrikzeichen
(Fabriksftempeln) Schwedens, Norwegens und Rußlands herrscht, scheint vorzüglich von
der erwähnten Eigenschaft der Continuität abzuhängen, und wenn man mit
Aufmerksamkeit die Manipulationen verfolgt, die in den verschiedenen Werkstätten mit
dem rohen Cementstahl vorgenommen werden, so begreift man augenbliklich, warum die
Fabrikanten auf die besagte Eigenschaft einen so hohen Werth legen. Die Erfahrung
lehrt, daß die Wände großer während des Cementirens entstandener Risse nur mit
großer Schwierigkeit durch fleißiges Gerben des Rohstahls vor seiner Verarbeitung
wieder vereinigt werden können. Sehr oft bleiben an den Stellen, wo die Risse
vorhanden waren, Unterbrechungen der Continuität, welche sich gewöhnlich durch graue
oder schwarze Fleke ankündigen. Diese Fleke, welche an der Oberfläche gegerbter
Stangen, selbst an roh bearbeiteten Objecten (Schneidewerkzeugen, Feilen u. s. w.)
nicht sichtbar sind, kommen doch bei der lezten feineren Bearbeitung (Poliren u. s.
w.) zum Vorschein, so daß man erst dann die Objecte als zum Ausschuß gehörig
erkennt, nachdem die ganze Arbeit umsonst an ihnen verschwendet worden.
Es gibt gewisse Eisensorten, welche im höchsten Grade die Neigung, zu Stahl zu
werden, besizen, und einen so brüchigen mit fehlerhaften Stellen versehenen Stahl
geben, daß wenigstens ⅓ der daraus verfertigten Objecte unter den Ausschuß
kommen muß. Die englischen Eisensorten, die man jezt in Yorkshire anwendet,
empfehlen sich gewöhnlich durch ihre vollkommene Continuität, und aus diesem Grunde
werden sie von den Stahlhütten zu gewissen Zweken gesucht, obgleich sie in Betreff
der Neigung zu verstählen den gemeinsten schwedischen und russischen Eisenzeichen
nachstehen.
Unter den übrigen Eigenschaften, welche die Fabrikanten von dem zu Stahl bestimmten
Eisen verlangen, will ich noch die Einförmigkeit in der Textur herausheben. Die
Stahlfabrikanten haben
mir oft Stangen als gleich gut zur Stahlerzeugung bezeichnet, wovon einige eine
halbblättrige, andere eine körnige und wieder andere eine dichtkörnige Structur mit
Uebergang ins Faserige und Sehnige zeigten; es ist aber immer vortheilhaft, wenn die
Structur in der ganzen Ausdehnung der Stange die nämliche ist. Im entgegengesezten
Fall erfahren die verschiedenen Partien der Stange während des Cementirens einen
verschiedenen Grad der Verstahlung, was nachher, um Stahl von einem bestimmten Grad
der Homogeneität zu erhalten, ein desto längeres Gerben nöthig macht, und somit die
Erzeugungskosten beträchtlich vermehrt.
Gestalt und Dimensionen der Eisenstangen. — Die zu
Stahl bestimmten Eisenstangen haben, mit Ausnahme einzelner Fälle, immer eine platte
Form, welche bei gleich großem Querschnitt der Stange sich der Cementation viel
besser fügt, als die quadratische oder runde. Die Stangen müssen stets eine ziemlich
beträchtliche Dike haben, damit die Kästen möglichst viel Eisen fassen; nur in
einzelnen Fällen weicht man von dieser Regel ab. Der Durchschnitt der Stangen
beträgt selten weniger als 6 Quadratcentimeter (2½ Quadratzoll) und steigt
oft bis auf 20 Quadratcentimeter (7½ Quadratzoll). Die Dike wechselt
gewöhnlich zwischen 0,008 und 0,020 Meter (3,6 und 9 Linien) und die größte
Dimension varirt zwischen 0,06 Meter (2¼ Zoll) und 0,140 Meter (5¼
Zoll).
Cementirpulver. — Mehrere Fabrikanten haben mich
versichert, daß die in den verschiedenen, über Stahlfabrication handelnden
Schriften, selbst in englischen Technologien, angegebenen Cementirpulver nie
allgemeine Anwendung fanden. Das einzige Reagens, das ich mit dem Eisen in die
Cementirkästen einsezen sah, ist Holzkohle, theils in Pulverform und theils als
kleine Stüke, deren Volum selten 2 Kubikcentimeter (9 Kubiklinien) übersteigt. Diese
Kohle wird aus den Aesten und Abfällen des in einem Umkreis von 35 Kilometer (etwa
½ deutsche Meile) um Sheffield geschlagenen Bauholzes, vorzüglich Eichenholz
bereitet. Die Kohle kömmt schon sehr verkleinert in den Hütten an und wiegt in
diesem Zustande 325 Kilogramme (?) (580 Pfd.) per
Kubikmeter (31,5 Kubikfuß); 100 Kilogramme (178½ Pfd.) kosten im Mittel 5,40
Frcs. Man hat oft, aber immer ohne guten Erfolg, versucht, die von einer
vorhergehenden Operation übrig gebliebene Kohle nach vorgenommenem Ausglühen als
Cementirpulver anzuwenden. Gewöhnlich vermengt man mit neuer frischer Kohle ¼
alter wieder ausgeglühter, und vermindert so etwas die Kosten, ohne die Kraft des
Cementirpulvers merklich zu verschlechtern.
Brennstoff zum Heizen der Oefen. — In Yorkshire wird nur allein
Steinkohle angewendet, sowohl beim Cementiren, als bei den übrigen Zweigen der
Stahlarbeit. Man gibt den gasreichen Kohlen, die im Feuer, ohne zu schmelzen,
zusammenbaken, den Vorzug und wendet ein Gemenge des Kohlenkleins und der Fragmente
an, die nach dem Aussuchen und Ausscheiden der großen Stüke zurükbleiben, wovon 100
Kilogr. 1–1,12 Frcs. kosten. Man könnte auch Kohlenklein schlechterer
Qualität, welches, in die Hütte gestellt, kaum 0,50 Frcs kosten würde, anwenden, man
würde hiedurch aber, ohne Vortheil, die Leitung des Processes nur verwikelter machen
und die beim Ankauf des Brennstoffes erzielte Ersparung würde durch die größere
Dauer des Processes und die Unregelmäßigkeit des Feuers aufgewogen werden. Eine
Kohlensorte, die mir als zum Heizen der Cementiröfen recht anwendbar bezeichnet
wurde, gab bei der Analyse in 1,000 Theilen 0,369 gasförmige Stoffe, 0,567
Kohlenstoff und 0,064 etwas eisenhaltige Asche.
Personal einer Cementstahl-Hütte. Die Führung eines
Cementirofens fordert zwei Leute, deren Arbeit in der Vorbereitung der Eisenstangen,
im Beschiken und Entleeren der Cementirkästen, und in der Leitung des Feuers während
der ganzen Operation besteht. Die Führung eines einzigen Ofens füllt die Zeit zweier
Arbeiter nicht aus; gewöhnlich können drei Arbeiter zwei Oefen in vollstem Gange
erhalten.
Beschikung des Ofens. Zuerst hauen die Arbeiter die zu
cementirenden Eisenstangen zu entsprechender Länge zu, indem sie dieselben 0,051
Met. (nahe 2 Zoll) kürzer machen als die Kästen lang sind. Ohne diese Vorsicht
würden die Stangen, die sich in der Hize stärker ausdehnen als die steinernen
Kästen, diese lezteren sicherlich zerreißen. Wenn ein Ofen nach gehöriger Abkühlung
und etwaiger Vornahme nöthig gewordener Reparatur frisch beschikt werden soll, so
begibt sich ein Arbeiter in denselben hinein, während ein anderer außerhalb das
Eisen und das Cementirpulver zulangt. Es wird dann auf den Boden des Cementirkastens
eine 0,08 Met. (3 Zoll) dike Schichte des Cementirpulvers und auf diese werden
hernach auf zwei verschiedene Arten abwechselnde Lagen von Eisenstäben und
Cementirpulver eingetragen. Entweder man legt die Stangen horizontal und auf die
breiteren Flächen neben einander und trennt sie durch 0,08 bis 0,015 Met.
(4–7 Linien) dike Kohlenschichten, oder man legt die Stangen horizontal auf
die schmäleren Flächen und trennt sie dann nur durch einige Millimeter (1–2
Linien) dike Cementirpulver-Schichten. Jede horizontale Eisenstangenlage wird
von der nächsten durch eine etwa 0,01 Met. (4½ Linien) dike
Cementirpulver-Schichte getrennt. Die Stangenstüke werden sorgfältig mit den
Enden an einander
gelegt und es wird bei der Einschichtung der Stangen und des Cementirpulvers darauf
gesehen, daß der von dem Eisen eingenommene Raum möglichst groß sey.
Wenn man bis zur Höhe der vier vorn erwähnten Seitenöffnungen gekommen ist, so legt
man daselbst Stangenstüke in der Art ein, daß man sie leicht herausziehen und nach
denselben den Fortschritt des Cementirprocesses beurtheilen kann. Den Schluß des
Einsazes bildet immer eine 0,08 Met. (3 Zoll) dike Lage des Cementirpulvers, welche
bis einige Centimeter (1–1½ Zoll) unter den obern Rand der
Cementirkästen reicht, und die Kästen werden nachher durch ein eben so einfaches als
wirksames Mittel hermetisch geschlossen. Ueber der lezten Kohlenlage applicirt man
nämlich eine 0,02 Met. (0,7 Zoll) dike Lage eines Mörtels, der aus der pulverigen
Masse, die sich unter den Schleifsteinen absezt, worauf die stählernen
Schneidwerkzeuge und andere Stahlartikel geschliffen und polirt werden, besteht.
Diese Masse, welche die Werkstätten Yorkshire's in Ueberfluß liefern, besteht im
Wesentlichen aus Quarzpulver, gemengt mit an der Oberfläche oxydirten
Stahltheilchen; sie erweicht sich durch Wirkung der Wärme, ohne jemals flüssig zu
werden.
Sind die Kästen so versorgt, so werden die zur Circulation der Flamme dienenden
Canäle gereinigt, es werden die zwei Thüren und die vier Eintragöffnungen mit
Ziegeln und Lehm verschlossen, ferner die Enden der zu den Probestangen führenden
Canäle zuerst mit Cementirpulver und nachher mit Lehm angefüllt, hierauf werden die
fünf Roststangen auf die dazu gehörigen Querstangen gebracht und endlich wird
angeheizt.
Anheizen des Ofens. Das Anheizen muß mit vieler
Behutsamkeit geschehen, wenn der Ofen neu oder ein Theil des Mauerwerkes erneuert
worden ist. Ist dieß nicht der Fall, so wird anfangs stärker geheizt, als im
Verlaufe des Processes, um die Kästen so schnell als möglich auf die Temperatur des
Rothglühens, bei welcher die Cementation erfolgt, zu bringen. Bei dem abgebildeten
Ofen dauert das Anheizen etwa 24 Stunden, und es wird dabei in einer Zeiteinheit 1
Quart Steinkohlen über den normalen Bedarf verbraucht.
Führung des Feuers. Die Geschiklichkeit des Arbeiters
besteht vorzüglich in einer solchen Regulirung und Leitung des Feuers, daß beständig
lebhafte Rothglühhize unterhalten, dieselbe aber nie überschritten werde. Diese
Temperatur, welche nahe dem Schmelzpunkte des Kupfers entspricht, ist weder zum
Schmelzen (Verglasen) der Ziegel, noch des ihnen als Bindemittel dienenden Lehms
hoch genug. Bei den meisten Oefen in Yorkshire findet man keine Register zur Veränderung des Zuges, so
daß der Arbeiter das Feuer nur durch fleißiges Ueberwachen und Versorgen des
Heizraumes (Herdes) leiten kann. Der Herd ist immer bis zum Niveau der Schwelle der
Eintragthüren mit Steinkohlen angefüllt, so daß die in Brand befindliche
Brennstofflage bei dem abgebildeten Ofen eine Dike von 0,3 Meter (11⅓ Zoll)
hatte. Diese Dike variirt aber je nach den Dimensionen des Ofens, nach der
Beschaffenheit des Zuges und vorzüglich nach der Qualität der Steinkohlen. Es ist
wichtig, daß die angegebene Dike der Brennstoffschichte nicht zu sehr abnehme, sonst
würde der Ofen sich abkühlen, und es ist deßwegen gut, von Stunde zu Stunde frischen
Brennstoff einzutragen. Während einer Post wird bei aschenreicher Steinkohle der
Rost zweimal gereinigt, und es muß diese Reinigung öfters wiederholt werden, wenn
die Temperatur des Ofens über die Massen zu sinken droht. Der Arbeiter macht den
Rost theilweise frei, wenn die Temperatur an beiden Enden des Ofens sich ungleich
entwikelt. Ein fleißiger Heizer kann die kurz vorher angegebene 0,3 Meter dike
Brennmateriallage im Herde auch auf eine Dike von 0,25–0,22 Met.
(9,4–8,2 Zoll) reduciren und so Brennmaterial sparen; in diesem Falle muß
aber öfter frischer Brennstoff aufgegeben werden und der Ofen ist bei Vergeßlichkeit
des Arbeiters mehr der Gefahr des Auskühlens ausgesezt. In Yorkshire, wo der
Brennstoff wohlfeil ist, wird nicht selten von 2 zu 2 Stunden frischer Brennstoff
aufgegeben und diese größern Intervallen haben zugleich den Zwek der Ersparung an
Handarbeit. Die Steinkohlen, welche länger anhalten als Holz, und welche bei einem
gegebenen Volum mehr brennbare Stoffe enthalten, eignen sich viel besser zum Heizen
der Cementiröfen als vegetabilische Brennmaterialien.
In den Cementiröfen von Yorkshire werden im Allgemeinen zu 100 Kilogr. (178½
Pfd.) Stahl 75 Kilogr. (nahe 133 Pfd.) Steinkohlen verbraucht. Bei einer Cementirung
von 17600 Kilogrammen (31433 Pfd.), wo auf die Leitung des Feuers besondere Sorgfalt
verwendet wurde, und wo das Feuer 8 Tage lang unterhalten worden, verbrannten am
ersten Tag 1600 Kilogr. (2858 Pfd.) Steinkohlen und an jedem folgenden Tag im Mittel
nur 1360 Kilogram. (2478 Pfd.); der Totalverbrauch betrug 11120 Kilogr. (19861
Pfd.), so daß auf 100 Kilogr. rohen Stahls 63 Kilogramme Steinkohlen kommen.
Das Feuer wird durch eine Anzahl Tage unterhalten, welche dem Querschnitt der zu
cementirenden Eisenstangen und dem Grade, in welchem man sie mit Kohlenstoff
verbinden will, proportional ist. Für einen Einsaz von 17600 Kilogr. variirt die
Dauer des Feuers zwischen 5 und 9 Tagen: die gewöhnliche Dauer ist 7 Tage; man muß aber bedenken, daß
das Cementiren noch ziemlich lange fortdauert, wenn auch kein Brennmaterial mehr
eingetragen wird, nämlich während der Zeit des Erkaltens.
Beendigung und Dauer des Cementir-Processes. Man
beendigt den Proceß damit, daß man den Ofen viel langsamer abkühlen läßt, als er
angeheizt worden, und man läßt zu diesem Ende die Schlaken sich so auf dem Roste
anhäufen, daß dieser vollständig verstopft wird. Dieß hat die doppelte Wirkung, daß
die Wärme sich im Ofen anhäuft, benüzt werden kann, und daß grellen
Temperatur-Veränderungen, welche die Dauer des irdenen Apparates vermindern
würden, vorgebeugt wird. Ist der Ofen unter die dunkle Rothgluth abgekühlt, so macht
man allmählich die verschiedenen Oeffnungen auf, um die Abkühlung durch frische Luft
zu beschleunigen. Gewöhnlich kann man 8 Tage nach dem lezten Eintragen von
Brennstoff den Ofen ausnehmen. Der Rohstahl wird bei den nämlichen sechs Oeffnungen,
die zur Beschikung der Kästen dienten, herausgenommen, zugleich wird die Reparatur
etwaiger kleinerer Beschädigungen am Ofen vorgenommen, was Alles gewöhnlich in einem
Tage geschieht, und dann ist der Ofen wieder zu einem neuen Einsaz bereit.
Physikalische Eigenschaften des Rohstahls. Durch die
Cementation werden die physikalischen Eigenschaften des Eisens gänzlich modificirt.
Es verschwindet die Hämmerbarkeit und die Stangen zerbrechen, wenn man sie aus
geringer Höhe auf die Kante eines Ambosses fallen läßt, und man kann sie durch einen
einfachen Schlag mit einem Handhammer in sehr kleine Stüke zerschlagen. Die
Oberfläche noch so gut geschmiedeter Stangen wird sehr ungleich; sie ist mit Bukeln
(Blasen) bedekt, und man sieht darauf überdieß deutlich die Kohlenstükchen
abgedrükt, mit welchen ihre Oberfläche in Berührung war. Im Querbruche der besten
Sorten des rohen Cementstahles bemerkt man unzählige, gewöhnlich den großen Flächen
der Stangen parallele Risse, die bei dem gemeinen Stahle sehr beträchtliche
Dimensionen erreichen nnd sich bis an die Oberfläche der Stangen erstreken. Die
Structur ist immer blätterig (lamellaire) und die
Blätter sind unvergleichbar größer, als man sie an gewissen Eisengattungen findet;
ihre größte Dimension beträgt oft mehr als 1 Cent. (4,5 Linie) und ihre Oberfläche
ist anstatt eben und glänzend, körnig und schuppig und reflectirt das Licht
schlecht. Auch der Bruch ist weniger glänzend als bei blätterigem Eisen. Endlich ist
die Farbe selbst sehr verändert; die bläuliche Nüance ist verschwunden und an ihre
Stelle ist eine weißgraue getreten.
Ein Cementirofen, welcher in möglich größter Thätigkeit erhalten wird, kann jährlich 20
Eiseneinsäze in Stahl verwandeln und eine Stahlhütte mittlerer Größe enthält drei
Oefen für drei verschiedentlich große Einsäze, nämlich von 12000 bis 15000
Kilogramm. (21432–26790 Pfd.), von 15000–18000 Kilogr. (26790 bis
32148 Pfd.) und 18000–22000 Kilogr. (32148–39292 Pfd.), so daß die
jährliche Erzeugung aller drei Oefen sich auf 10000 metrische Centner beläuft. Die
seit einigen Jahren ungünstigen Verhältnisse des Stahlhandels in Yorkshire sind
Ursache, warum dieses Maximum der Erzeugung von den Hütten daselbst bei weitem nicht
erreicht wird. Im Jahre 1842 erzeugten die 97 Cementiröfen von Yorkshire in 33
Hütten vertheilt, zusammen 165000 metrische Centner Stahl, so daß auf eine Hütte mit
drei Oefen im Mittel nur 5000 metrische Centner kommen. Mehrere Fabrikanten
stählerner Objecte bereiten sich den Stahl, den sie verarbeiten, in eigenen Hütten;
die meisten Stahlhütten sind in den Händen kleiner Fabrikanten, die nur den Stahl
erzeugen, nicht aber selbst verarbeiten; leztere befinden sich in weit weniger
günstigern Verhältnissen.
Fabricationskosten. Jede metallurgische Unternehmung faßt
zwei gewöhnlich ziemlich stark unterschiedene Abtheilungen in sich, welche in
Großbritannien manchmal vollständig getrennt sind: nämlich den commerciellen Theil,
welcher den Ankauf der zu verarbeitenden Mineralien oder Metalle und den Verkauf der
erzeugten Fabricate besorgt und durch dessen Gewinn die Kosten, die Fondsvorschüsse
und die ungünstigen Chancen gedekt werden müssen, die mit dem Einkauf und Verkauf
verbunden sind; dann den eigentlichen industriellen Theil, durch dessen Gewinn die
Fabricationskosten gedekt werden müssen. Die erste Regel für jeden Metallurgen ist,
diese beiden Arten von Kosten so viel als möglich von einander zu trennen. So muß
bei dem jezigen Stand der Stahlindustrie in Yorkshire ein Industrieller, welcher
zugleich Kaufmann und Fabrikant ist, per 100 Kilogr.
(178,6 Pfd.) rohen Cementstahl bei 12 Fr. für die Kosten und den Gewinn rechnen. Der
eigentliche Fabrikant, der sich nur allein mit der Verwandlung des Eisens in Stahl
befaßt, erhält gewöhnlich für das nämliche Product 3,53 Fr., so daß die Kosten und
der Gewinn für jede der beiden Abtheilungen sich so herausstellen: für den
Fabrikanten 3,53 Fr. und für den Kaufmann bei 8,47 Fr.
Die nachstehende Tabelle gibt ein näheres Detail über die Kosten und den Gewinn einer
Cementstahlhütte in Yorkshire, welche, wie dieß bei den meisten dortigen Stahlhütten
der Fall ist, für Rechnung eines Andern das ihr zu diesem Ende anvertraute Eisen
verarbeitet, welche in drei Cementiröfen jährlich 6000 Cntr. rohen Cementstahl
erzeugt:
Textabbildung Bd. 091, S. 461
Materialverbrauch und Arbeitstage
per 100 Kilogramme.; Werth der Materialien und Arbeitstage in Francs.;
Partielle.; Totale.; Eisen zum Cementiren 99,1 Kilogr.; Holzkohle, 100 Kilogr.
Zu 5,40 Fr 5,5 Francs; Steinkohle, 100 Kilogr. Zu 1,06 — 75,0 —;
Handarbeit, taͤglich mit 3,62 — 0,20 Tage; Industrielles Capital:
Miethe der Huͤtte oder Interessen des Capitals à 5 Proc; Im Umlauf
befindliche Fonds: Interessen zu 6 Proc; Erhaltungskoften: Fuͤr Ziegel,
Lehm, Eisen zu den Werkzeugen und Tagloͤhne für besondere Arbeiter; Die
Leitung und Aufsicht besorgt der Oberarbeiter unentgeltlich.; Verschiedene
Auslagen, d. i. Abgaben und Patente, Briefporto, Kanzleikosten u. s. w; Gewinn;
Zusammen 3,53
Der mittlere Preis des in Yorkshire zur Stahlfabrication angewendeten Eisens ist
beiläufig 18 Pfd. St. per Tonne, oder in runder Zahl 45
Fr. für 100 Kilogr. Der Preis für 100 Kilogr. rohen Cementstahl stellt sich somit
auf 48,13 Fr. heraus: 99,1 Kil. Eisen à 45 Fr. kosten 44,60 F.; 75 Kilogr.
Steinkohle à 1,06 Fr. machen 0,80 Fr.; die Handarbeit à 3,62 Fr. täglich macht für
0,20 Fr. eines Tages 0,72 Fr., und die andern Auslagen belaufen sich auf 2,01 Fr.,
was zusammen 48,13 Fr. ausmacht.
Der Fabricationspreis von 3,53 Fr. für 100 Kilogr. Stahl bleibt bei allen
Handelsverhältnissen unverändert der nämliche, mit Ausnahme gewisser specieller
Conventionen, und dieß ist die Folge der Scheidung der Interessen der verschiedenen
Classen von Industriellen, welche zur Fabrication bestimmter Producte in den Hütten
von Yorkshire concurriren.
Diese Vertheilung der Arbeit übt einen sehr glüklichen Einfluß auf das Ganze der
Stahlfabrication und beugt den so nachtheiligen Schwankungen des Preises vor, wie
sie sich z. B. während der lezten Jahre auf so verdrießliche Weise in den
Eisenhütten zeigten.
(Fortsezung folgt.)
Tafeln
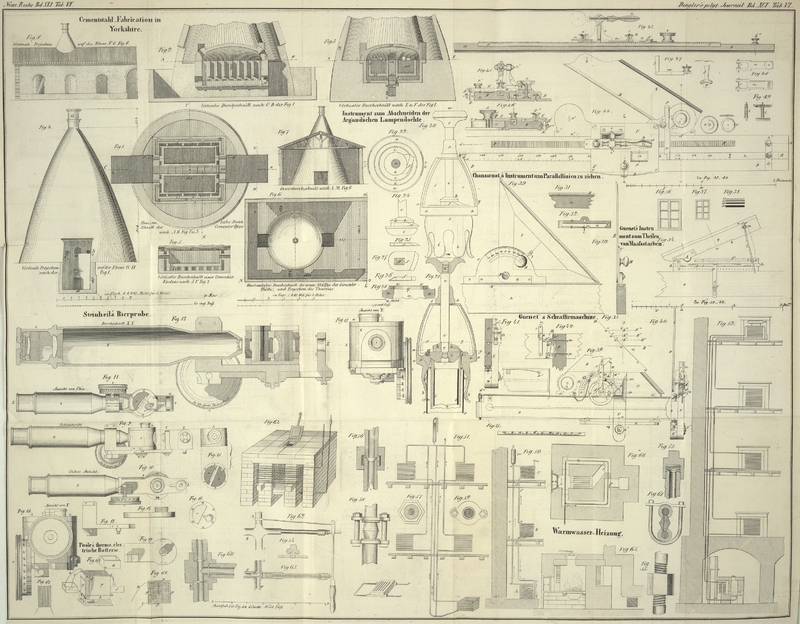