Titel: | Ueber die Gewinnung von Zellstoff für Papier. |
Fundstelle: | Band 261, Jahrgang 1886, S. 379 |
Download: | XML |
Ueber die Gewinnung von Zellstoff für
Papier.Ueber die Darstellung von Holzzellstoff auf chemischem
Wege hat Prof. E. Hoyer eine ausführliche
Uebersichtsabhandlung im Bayerischen Industrie- und
Gewerbeblatt, Vierteljahrschrift 1885 * S. 53 ff. veröffentlicht. (Vgl.
auch Papier-Zeitung, 1885 * S. 1262 ff. Glaser's Annalen, 1885
Bd. 17 * S. 191 ff.)
(Patentklasse 55. Fortsetzung des Berichtes Bd.
258 S. 312.)
Mit Abbildungen auf Tafel
25.
Ueber die Gewinnung von Zellstoff für Papier.
In einem Vortrage über die Verwendung von Holz zur
Herstellung von Papierstoff behandelte T. A. Reid(Journal of the Society of Chemical Industrie, 1886 S. 273) hauptsächlich
das Natronverfahren.
Die Eignung der verschiedenen Holzarten wurde durch folgende
Erfahrungswerthe gekennzeichnet:Vgl. auch G. Hofmann: Papierfabrikation, 1875 S.
520.
Zellstoff
Faserlänge
Buche
38,5 Proc.
kurz
Birke
42,0
„
Hemlocktanne
37,5
lang
Pappel
41,0
mittel
Fichte
39,0
lang
Tanne
38,0
„
Nach Reid's Erfahrung soll das Kochen
des Holzes mit einer Lauge von 20 Procent des Holztrockengewichtes Gehalt an 70
procentigem Aetznatron bei einer Dampfspannung von 8at, entsprechend einer Temperatur von 171°, günstige Ergebnisse liefern.
Nach etwa 2 stündigem Kochen unter dieser Spannung wird die Lauge abgelassen und der
Kocher mit heiſsem Wasser gefüllt. Die aufgelösten Holzstückchen läſst man dann mit
der Flüssigkeit des Kochers in hölzerne Absetzgefäſse ab und wäscht darauf den Stoff
aus.
Zur Wiedergewinnung des Natrons aus den Abfallaugen soll nur die
erste Lauge verwendet werden, welche 1,09 bis 1,1 sp. G. besitzt und etwa 90 Procent
der ursprünglich benutzten Soda enthält. Die Lauge wird abgedampft (vgl. * S. 260 d.
Bd.) und dann geröstet, um die organischen Bestandtheile zu verbrennen. Man erhält
eine Soda von etwa 85 Proc. Gehalt an Na2CO3 (50 bis 53 Proc. Natron), welche noch etwas
Natriumsulfat und Sulfit enthält. Diese Soda wird zu einer Lauge von 1,1 sp. G.
gelöst und mit Kalk kausticirt. Auf diese Weise gehen allerdings die organischen
Bestandtheile der Lauge für eine Verwerthung (vgl. 1885 258 334. 1886 261 275) verloren. Besser wäre
wohl eine Destillation der abgedampften Masse in Retorten, wobei Essigsäure u. dgl.
gewonnen werden könnten. Im Durchschnitte werden aus den Laugen etwa 80 Procent des
benutzten Alkalis wiedergewonnen, was die Kosten für dasselbe um etwa 50 Proc.
verringert.
Reid macht noch folgende Angaben über
die Herstellungskosten von Zellstoff aus Holz und aus
Espartogras:
Holz
3t Holz
zu 25 M. für 1t
75,00 M.
Mechanische Bearbeitung, 7,50 M. für 1t
22,50
Aetznatron, 25 Proc. des Holzgewichtes, 20
M. für 100k
150,00
Waschen, Bleichen u.s.w., 5 M. für 1t
15,00
––––––––
262,50 M.
20 Proc. unvorhergesehene Kosten
52,50
––––––––
315,00 M.
50 Proc. des Sodawerthes
wiedergewonnen
75,00
––––––––
240,00 M.
1t
Natron-Holzzellstoff kostet also 240 M., wenn angenommen wird, daſs das Holz nur ⅓
seines Gewichtes Zellstoff ergibt.
Espartogras, wobei angenommen wird, daſs dasselbe die Hälfte
seines Gewichtes Zellstoff ergibt:
2t
Esparto zu 120 M. für 1t
240,00 M.
Mechanische Behandlung, 5 M. für 1t
10,00
Aetznatron, 10 Proc. des
Espartogewichtes
40,00
Waschen, Bleichen u.s.w., 3 M. für 1t
6,00
––––––––
296,00 M.
10 Proc. unvorhergesehene Kosten
29,60
––––––––
325,60 M.
50 Proc. Soda wiedergewonnen
20,00
––––––––
1t Esparto-Zellstoff kostet daher
305,60 M.
Carl Ferd. Dahl in Danzig (Oesterreichisch-Ungarisches
Patent vom 19. Oktober 1884) gibt ein Verfahren zur Gewinnung von Zellstoff aus Holz, Stroh, Alfa u.s.w. durch Kochen mit
einer Lösung, welche Natriumsalze in vier verschiedenen
Verbindungen, als schwefelsaures und kohlensaures Natron, Natronhydrat und
Schwefelnatrium, enthält, ferner ein Verfahren zur Bereitung der Kochlösung
aus schwefelsaurem Natron und dem aus den Kochlaugen wiedergewonnenen gleichen
Stoffe durch Kochen mit Kalk an. Das Kochen wird in schmiedeisernen Gefäſsen ohne
Bleiauskleidung unter Dampfdruck vorgenommen und erfordern 100k mitteltrockenes Kiefernholz etwa 26k, Stroh, Alfa und Esparto 10 bis 12k obiger Salze in Lösung.
Kiefern-, Fichten- und Tannenholz erfordern 5 bis 10at Dampfdruck, wobei die Stärke der Natriumsalzlösung 6 bis 14° B., die
Kochzeit 30 bis 4 Stunden beträgt. Stroh, Alfa und Esparto erfordern 2 bis 5at Dampfdruck, Stärke der Natriumlösung 5 bis 8°
B. und eine Kochdauer von 8 bis 3 Stunden.
Nach beendeter Kochung wird die braunschwarze Lauge behufs späterer Wiedergewinnung
der Natriumsalze in eiserne Behälter abgeblasen, der zurückbleibende Zellstoff
entweder im Kocher, in Shanks'schen Kästen o. dgl. mit
warmem Wasser ausgewaschen, im Holländer in bekannter Weise zu Papierbrei
verarbeitet und mit Chlorkalklösung gebleicht. Die Farbe des ungebleichten Stoffes
ist graugelblich, die des gebleichten Stoffes hochweiſs oder schwach, aber rein
gelblich, je nach dem Grade der Bleiche.
Zur Darstellung der Natriumlösung dient schwefelsaures
Natron (Natronsulfat). Das Sulfat wird, in Wasser aufgelöst, mit 20 bis 23 Proc.
gebranntem Kalk gekocht. Die in dieser Weise bereitete Lauge ist schon zum Kochen
brauchbar, erhält jedoch ihre richtige Zusammensetzung durch Zugabe der aus der
Sulfatlösung nach dem Kochprozesse wiedergewonnenen Salze. Die gebrauchte Lauge wird
zur Wiedergewinnung im Abdampfofen eingedickt, stark calcinirt und nach
stattgefundener Entgasung aus dem Ofen gescharrt, dann ausgewaschen und die Lösung
zum Bereiten neuer Lauge verwendet. Zur Gewinnung reiner Salze ohne
Kohlenbeimischung zieht man die eingedickte Lauge aus dem Abdampfofen heraus und
läſst dieselbe im Schmelzofen bei dunkler Rothglut abbrennen. Die geschmolzene Masse
nimmt nach dem Erkalten eine rothbraune Färbung an, ist in Wasser leicht löslich und
hat annähernd folgende Zusammensetzung: 16 Proc. schwefelsaures Natron, 50 Proc.
kohlensaures Natron, 20 Proc. Natronhydrat, 10 Proc. Schwefelnatrium, 4 Proc.
verschiedene unwesentliche Stoffe. Diese Zusammensetzung ist sehr veränderlich, je
nach den Eigenschaften des gekochten Materials, jedoch ohne die auflösende Kraft der
daraus später hergestellten Lösung zu beeinträchtigen.Das wiedergewonnene Salz ist baldmöglichst aufzulösen oder den Einflüssen der
atmosphärischen Luft zu entziehen. Durch den Koch- und
Wiedergewinnungsprozeſs gehen 10 bis 15 Procent der in Lösung gewesenen
Salze verloren. Im gewöhnlichen Betriebe ersetzt man bei der Laugenbereitung
den Verlust durch schwefelsaures Natron. Es kommen zur Auflösung 85 bis 90
Proc. wiedergewonnenes Salz, 15 bis 10 Proc. Sulfat, welche Mischung, mit 20
bis 23 Proc. gebranntem Kalk gekocht, die richtige Lauge gibt.Bei 10 Proc. Verlust nimmt man zur Bereitung der Kochlauge eine abgeklärte,
Wasser haltige Lösung, in welcher 90k
wiedergewonnenes Salz enthalten sind, setzt 10k Sulfat zu und kocht die Lösung, in welcher 100k Salze in vorbeschriebenem Verhältnisse
enthalten sind, mit 20k gebranntem
Kalk.Beträgt der Verlust 15 Proc., so kommen auf 85k wiedergewonnenes Salz 15k
Sulfat, welche mit 23k Kalk gekocht
werden.Bei 20 Proc. Verlust gelangen 80k
wiedergewonnenes Salz, 20k Sulfat zur
Auflösung, die man mit 25k Kalk
zusammenkockt.Will man 25 Proc. Sulfat zusetzen, so kommen 75k wiedergewonnenes Salz, 25k
Sulfat und 28k gebrannter Kalk zur
Auflösung. Bei gleichmäſsigem Betriebe soll die äuſserste Grenze des
Zusatzes an Sulfat 30 Proc. betragen: 70k
wiedergewonnenes Salz, 30k Sulfat, 32k gebrannter Kalk.
Das Verhältniſs der in der Kochlösung enthaltenen Salze ist durchschnittlich: 37
Proc. schwefelsaures Natron, 8 Proc. kohlensaures Natron, 24 Proc. Natronhydrat, 28
Proc. Schwefelnatrium, 3 Proc. verschiedene Verbindungen. Diese Zusammensetzung ist
sehr veränderlich, je nach den Eigenschaften des zu kochenden Materials. Die
Ueberführung des bekannten Soda- bezieh. Natronhydrat-Verfahrens in das beschriebene
Sulfatverfahren geschieht in der Weise, daſs man bei der Laugenbereitung den Verlust
des Natronhydrates durch Sulfat statt durch Soda ersetzt und dann allmählich mit dem
Schwinden des Hydrates die Zugabe an Kalk beim Kochen der Lösung von 45 Proc. auf 20
bis 23 Proc. herabmindert.
Bei dem Natron-Verfahren zur Herstellung von Zellstoff
will C. A. Hesse in Dampfsägewerk Zellwald bei Siebenlehn in Sachsen (* D. R. P. Nr. 35854 vom 15. August 1885) die chemische Behandlung und darauf folgende mechanische Bearbeitung in einem Apparate vornehmen. Die hierzu benutzte Verbindung eines Kochers mit den Mahlvorrichtungen für die weich gekochten
Holzstücke veranschaulicht Fig. 20 Taf. 25. Der
stehende cylindrische Kochkessel a besitzt einen
Siebboden b, über welchem das auf der Achse w befestigte Schaufelkreuz c wegstreicht und dabei die weichen Holzstücke durch die Oeffnungen des
Bodens drängt. Am unteren Ende der Achse w sitzt eine
Kurbel d, welche den Quetschklotz e an der Wand des Trichters e1 herumführt (vgl. Motte's Mörsermühle 1878 227
* 57), wodurch die kleinen Holzstückchen zerdrückt werden. Der Klotz e stützt sich auf einen Kugelzapfen und letzterer ist
in der Höhe verstellbar, um sowohl das Zerquetschen zu regeln, als den Kocher unten
abzuschlieſsen. Hierzu liegt das den Zapfen tragende Kreuz f mit seinem nach einer Schraubenlinie geformten Rande auf einem gleich
geformten Absatze des Cylinders g auf. Wird das Kreuz
f mittels des Zahnrades h verdreht, so bewegt sich f und damit der
Kugelzapfen auf und ab. Damit dabei die Zähne von h
nicht aus der Verzahnung des Kreuzes f treten, verläuft
die Verzahnung des Rades h spiralförmig. Auf der
wagerechten, in dem Lager p unverschiebbar gehaltenen
Achse l sitzt der mit gewundenen Riffelungen versehene
Kegel n, welcher sich in einem gleich geriffelten
Hohlkegel m dreht. Durch die Verschiebung des Lagers
p mittels der Schraube o kann der Zwischenraum der Mahlflächen von n
und m verändert werden. Von den mit dem
Dampfstrahlapparate q verbundenen Rohrleitungen führt
t in den Laugenbehälter L,
u nach einem Abfluſskanale und y nach dem
Dampfkessel.
Das Verfahren mit diesem Apparate
soll nun folgendermaſsen verlaufen: Nachdem der Kocher a mit zerkleinertem Holze angefüllt und die Halbkugel des Quetschwerkes
dampfdicht gegen den Kugelsitz geschraubt ist, öffnet man die Ventile v1, v2, v3 und treibt mittels
des Dampfstrahlapparates q die Lauge aus dem Behälter
L in den Kocher, bis dieselbe durch den Hahn x ausflieſst, welcher darauf sammt den Ventilen v2 und v3 geschlossen wird.
Durch weitere Einführung des Dampfes wird die Lauge eine Zeit lang im Kochen
erhalten und dann durch die Ventile v3, v5 und v2 abgelassen. Hiernach wird Ventil v5 und v6 geschlossen, Ventil
v1 und v4 geöffnet und mit dem
Dampfstrahlapparate ein Gemisch von Dampf und heiſser Luft, deren Temperatur weit
über der Temperatur des gesättigten Dampfes liegt, eingeführt. Der auf diese Weise
überhitzte Dampf von etwa 5at Spannung soll
leichter in die Zellen des Holzes eindringen und die verholzten Zellwände auflösen.
Sobald eine entnommene Probe zeigt, daſs das Holz genügend aufgeschlossen ist, wird
der Klotz e etwas niedergelassen und das Quetschwerk
sowie der Kegel n in Umdrehung versetzt. Die Holzstücke
werden nun von dem Rührer c durch die Löcher im Boden
b hindurchgedrängt und fallen durch den Trichter in
das Quetschwerk, wo sie vollständig zerquetscht durch das Kreuz f zum Kegel n gelangen.
Die zwischen diesem Kegel n und dem Mantel m zerfaserte dickbreiige Masse wird durch den Stutzen
s1 hinausgedrückt.
Durch die Leitung s2
tritt der Dampf aus, welcher noch zur Heizung des Trockenraumes verwendet werden
kann.
Bei Herstellung von Zellstoff mittels Sulfiten soll bei
dem Verfahren von Eugen Baron Ritter und Karl
Kellner in Podgora bei Görz, Oesterreich (Nordamerikanisches Patent Nr.
329214 vom 27. Oktober 1885) zur vollen Ausnutzung der
Säuren (vgl. 1884 252 327) dieselbe in zwei oder
mehreren zusammen arbeitenden Kochern nach einander benutzt werden. In Fig. 10 Taf.
25 sind A und B zwei
Kocher aus Eisen mit innerem Bleimantel. Der Behälter C
enthält die Lösung von Schwefligsäure, der Behälter D
frisches Wasser. Ein Rohr d führt von C und D durch Abzweigungen
e und f mit Ventilen
m und n in die beiden
Kocher; die Rohrzweige e und f münden ein wenig über den Gittern a und b, welche das Holz in die Flüssigkeit getaucht halten.
Das Rohr g steht nach rechts mit einem Dampfkessel und
einem Kessel mit Schwefligsäure in Verbindung und endigt links bei c in eine Abfluſsrinne. Das Rohr g hat zwei Abzweigungen i
und h, welche in den Bodentheil der Kocher treten, wo
sie mit Ventilen k und l
verschlossen sind. Auſserdem hat das Rohr g zwei
Abzweigungen o und p,
welche ebenfalls Ventile haben und oben in den Kochern enden. Zum Entleeren der
Kocher dienen die Ablässe r und s.
Zur Erklärung des Arbeitsvorganges sei angenommen, der Kocher A enthalte Holz, welches schon der Einwirkung von 2 mal gebrauchter
Säurelösung unterliegt, während der Kocher B mit
frischem Holze gefüllt ist. Man öffnet die Ventile m, k
und l, während die Ventile n,
o, p, q und r geschlossen bleiben. Die frische
Lösung läuft also durch das Rohr e nach A und drängt die dort gebrauchte Lösung durch die
Röhren i, g und h in den
Kocher B. Wenn A mit
frischer Lösung gefüllt ist, wird das Ventil m
geschlossen und r geöffnet, worauf Dampf durch die
Rohre i und h in beide
Kocher eintritt und auf das Holz einwirkt. Wenn das Kochen in B beendet ist, wird das Ventil r wieder geschlossen und die Ventile p und
q geöffnet. Die Schwefligsäure und der Dampf werden
durch p und das Rohr g in
die Abfluſsleitung c geblasen oder behufs
Wiederverwendung in geeigneten Apparaten behandelt. Hierauf wird alle Flüssigkeit
durch Ablaſs s aus dem Kocher B entfernt, in welchem sich jetzt nur noch theilweise aufgelöstes Holz
befindet. Die Lösung vom Kocher A wird dann durch
Zulassen von frischem Wasser aus dem Behälter D auf dem
früheren Wege in den Kocher B getrieben und ist jetzt
einmal benutzte Lösung. Darauf wird das Kochen wiederholt, dann die Röhren e, o und i abgesperrt, der
Kocher A geleert und mit frischem Holze gefüllt. Von
jetzt ab wiederholt sich das Verfahren, nur tauschen die beiden Kocher die
Rollen.
Nach einem zweiten Patente Nr. 329215 der Genannten soll das Auflösen des Holzes und das Bleichen der
erhaltenen Fasern in den Kochern wie bisher getrennt, jedoch in einem ununterbrochenen Vorgange ausgeführt werden. Um aus
Holz sehr weiſse und starke Fasern zu erhalten, soll dasselbe in senkrecht stehenden
Kesseln, welche die lösende Flüssigkeit enthalten, eingeweicht und vor der Erhitzung
Schwefligsäure so lange
eingepreſst werden, bis ein Druck von wenigstens 2at erreicht ist. Dann erst wird entweder Dampf oder Dampf mit
Schwefligsäure gemischt unter einer Temperatur über Siedehitze längere Zeit
eingeleitet, bis die Spannung etwa 3 bis 5at
erreicht hat. Hierdurch erfolgt zunächst Auflösung des Holzes, dann Bleichen der
Faser. Der Stoff wird weiſs, enthält keine harten Bestandtheile und kann weiter
verarbeitet werden, ohne einen Knotenfänger zu gebrauchen. Der Kochprozeſs dauert
etwa 14 bis 18 Stunden; doch kann derselbe bei niedrigem Drucke bis auf 36 Stunden
verlängert werden. Zur Ausführung des Verfahrens werden wie vorher zwei oder mehrere
zusammenarbeitende Kocher benutzt; bei hartem Holze werden Drehkocher empfohlen.
Zur Herstellung von Zellstoff nach dem Sulfit- oder nach
dem Natronverfahren benutzen J.
D. Tompkins in Nassau, J. Arkell in
Canajoharie und Ch. Wetherwax in Albany
(Nordamerikanisches Patent Nr. 340640) einen stehenden
cylindrischen, oben und unten kugelförmig geschlossenen Kocher A (Fig. 11 Taf. 25), welcher
oben und unten einen Siebboden B und B1 besitzt. Die Wirkung
der verschiedenen zur Anwendung kommenden Flüssigkeiten soll erhöht und damit der
Prozeſs beschleunigt werden durch eine abwechselnd nach
beiden Richtungen erfolgende StrömungUm in Holzkochern eine Strömung der Kochflüssigkeit zu erzeugen, benutzen Gebrüder Körting in Hannover, wie Prof. Hoyer im Bayerischen
Industrie- und Gewerbeblatt, 1885 * S. 80 berichtet, einen Injector, welcher an der Seite des Kochers
stehend angebracht wird und dessen Ein- und Auslauf durch Rohre mit dem
Boden und Deckel des Kochers in Verbindung steht. Durch Einlassen von Dampf
von mindestens 1at Ueberdruck über die
Kesselspannung wird dann eine Strömung der Flüssigkeit im Kocher von oben
nach unten hervorgerufen. derselben. Hierzu sind zwei Flügelpumpen P1 und P2 bestimmt, welche
durch Rohrleitungen c und d so mit den Hohlräumen unter den Siebboden B
und B1 in Verbindung
stehen, daſs die Pumpe P1 eine Strömung von unten nach oben, die Pumpe P2 eine Strömung von oben nach unten in
dem Kocher A erzeugt. Durch Wechsel weises Ein- und
Ausrücken der beiden Pumpen P1 und P2 wird
die Strömungsrichtung nach Ablauf bestimmter Zeiten immer geändert. In die Leitungen
c und d der Pumpen
führen gleich die Zuleitungsrohre für die verschiedenen Flüssigkeiten. Durch das
Rohr b wird Dampf in die Hohlräume der Boden behufs
Reinigung der Sieböffnungen geblasen. Die Dampfzuleitung in den Kessel A erfolgt durch das Rohr a. Das Steigrohr d der Pumpe P2 läuft in ein im
oberen Bodenraume liegendes rundes Siebrohr aus.
Das Holz, Stroh u. dgl. wird in den Kessel A durch das
obere Mannloch gefüllt und zuerst mit heiſsem Wasser ausgewaschen; hierauf nimmt die
Behandlung mit der Lauge oder Säure ihren Anfang, wobei hauptsächlich eine Strömung
von unten nach oben eintreten soll. Nach dem Auswaschen des gelösten Holzes mit
heiſsem Wasser wird dann gleich das Bleichen ebenfalls in dem Kocher A vorgenommen.
In Bezug auf die Einrichtung der Kocher für das
Sulfitverfahren sind folgende Neuerungen zu verzeichnen.
Ch. S. Wheelwright in Providence (Nordamerikanisches
Patent Nr. 337720 und Nr. 337721) setzt einen Kocher
aus unter einander durch eine groſse Zahl Schrauben verbundenen Ringstücken zusammen (vgl. Fig. 19 Taf. 25).
Besonders zu erwähnen ist die Befestigung der Bleiauskleidung an den
Verbindungstellen der Ringstücke. In Fig. 17 Taf. 25 ist ein
Bleiring von H-förmigem Querschnitte, dessen Hohlräume mit Gummi ausgefüllt sind,
zwischen die Flanschen gelegt, so daſs der innere Druck im Kessel mit abdichtet.
Nach Fig. 18
werden die Ränder der Bleibleche einfach umgebördelt in Spuren an den Flanschen
gelegt und beim Zusammenschrauben fest auf einander gepreſst. Die Einbiegung der
Ringstücke nach innen und die damit erhaltene gebogene Lage der Bleibleche dürfte
dem gröſseren Ausdehnungsbestreben derselben gegenüber den eisernen Ringen Rechnung
tragen und dadurch einem Aufreiſsen der Bleiverkleidung an den Trennungsstellen der
Bleche wirksam entgegen wirken.
Ch. E. Ball in New-York (Nordamerikanisches Patent Nr.
336078) läſst die Bleiauskleidung von der eisernen
Blechwand des Kochers etwas abstehen und stützt die
erstere durch am Bleibleche vorstehende Rippen oder Stehbolzen. Der Raum zwischen
dem Blei- und Eisenmantel wird mit Dampf gespeist; jedoch findet die Heizung der
Lauge im Kocher durch unmittelbare Einleitung von Dampf statt. Um Zerstörungen des Eisenmantels durch in dem
Zwischenräume des Doppelmantels vermöge Undichtheiten der Bleiauskleidung sich
ansammelnde Lauge rechtzeitig vorzubeugen, ist durch
diesen Zwischenraum an der tiefsten Stelle desselben der Leitungsdraht einer elektrischen Batterie gelegt, welche beim Drücken eines
Knopfes eine Glocke zum Ertönen bringt. Durch die zeitweise erfolgende Schlieſsung
des Batteriestromes hat man ein Mittel, das Vorhandensein von Lauge nachzuweisen, da
dieselbe den schwachen Leitungsdraht bald durchfriſst und dann die Glocke nicht mehr
ertönt. (Vgl. auch Ball * D. R. P. Nr. 36976 vom 16.
Februar 1886.)
Auf gleiche Weise wie J. Makin (vgl. 1885 258 318) will auch G. W.
Russell in Lawrence (Nordamerikanisches Patent Nr. 341434) Blei-platten für Sulfitkocher-Auskleidungen herstellen.
Um dabei die mit der Eisenplatte auf einer Seite verbundene Bleidecke gegen ein
Loslösen besser zu sichern, erhält nach Fig. 15 und 16 Taf. 25 die
Eisenplatte mit Köpfen versehene Stifte oder dieselbe wird einem Reibbleche ähnlich
gelocht und die erzielten Schuppen hakenförmig umgebogen. Nach einem zweiten Patente
Nr. 341435 soll ein Drahtgewebe mit Blei umgössen
werden (vgl. Fig.
14).
Zur Befestigung solcher Bleifutterplatten in den
Kochern, welche, wenn die letzteren cylindrisch sind, mittels verlötheten Ringen
erfolgt, benutzt Ch. Springer in Boston (* D. R. P. Nr.
35112 vom 22. August 1885) durch Schrauben festgehaltene Leisten, daher diese Art
der Befestigung namentlich für kugelförmige Kocher berechnet sein
dürfte. Wie in Fig.
13 Taf. 25 veranschaulicht ist, werden die Fugen zwischen den einzelnen
Platten mit Asbest o. dgl. ausgefüllt und dann von auf Makin'sche Art verbleiten Metallstreifen s
überdeckt, welche durch die mit verbleiten Köpfen versehenen Schrauben t festgehalten werden.
Den von A. Leonhardt angegebenen Apparat zum Reinigen von Sulfit-Zellstoff (vgl. 1885 258 318) hat Prof. Mitscherlich in Freiburg
i. B. in Nordamerika unter Nr. 344323 patentirt erhalten. Hiernach erhält das
Schwimm sieb längliche Oeffnungen und der aus dem Stoffabsonderer kommende, ziemlich
trockene Stoff soll auf einem endlosen Bande nach einer Bütte geleitet, dort
nochmals mit Wasser verdünnt und dann zur Entwässerung auf eine Langsiebmaschine
gebracht werden. Von der letzteren wird die erhaltene Stoffbahn zwei
Trockencylindern zugeführt, um nach einem abermaligen Auspressen zwischen einem
Walzenpaare aufgewickelt zu werden. Die Eisentheile des Apparates sind zu verbleien,
da sonst der Stoff gefärbt wird, indem die immerhin noch vorhandenen Säurespuren das
Eisen angreifen, auch wenn das Wasser selbst nicht Eisen haltig ist.
Zum Sortiren des zerquetschten Zellstoffes von
Asttheilchen u. dgl. bringt Ch. Wandel in Reutlingen
den in Fig.
12 Taf. 25 im Durchschnitte dargestellten Apparat zur Ausführung, welcher im Wesentlichen einem rotirenden
Knotenfänger gleicht und sich nach der Papierzeitung,
1886 * S. 1070 bereits verschiedentlich bewähren soll. In dem Troge B, in welchen die Zellstoffmasse bei A zuläuft, dreht sich, vollkommen in derselben
eintauchend, der mit durchgehender Achse a versehene
Siebcylinder T ohne Schüttelung mit 40 bis 50 Umgängen
in der Minute, also ziemlich rasch. Durch die feinen, bis zu 0mm,3 weiten Schlitze des Siebcylinders dringen die
Fasern mit der Flüssigkeit in das Innere des Cylinders und laufen aus demselben
seitlich bei o in die Rinne C ab, um aus dieser auf die Entwässerungsmaschine zu gelangen. Im Inneren
des Cylinders T sind Schaufeln s angebracht, welche den Durchgang durch die Siebfläche wesentlich
unterstützen sollen.
Tafeln
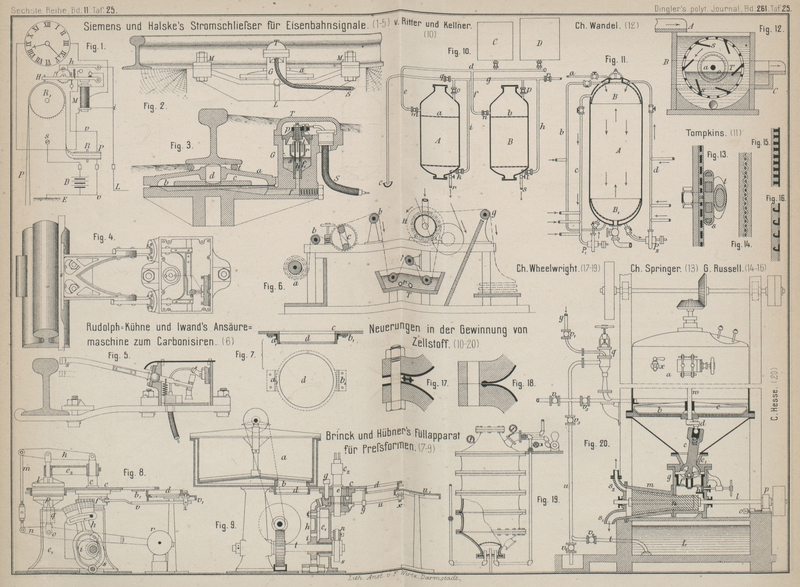