Titel: | Verfahren und Einrichtungen zum Trocknen, Sortiren und Zerkleinern von Kohlen, sowie zur Herstellung, zum Kühlen und Löschen von künstlicher Kohle. |
Autor: | W. Koort |
Fundstelle: | Band 270, Jahrgang 1888, S. 193 |
Download: | XML |
Verfahren und Einrichtungen zum Trocknen,
Sortiren und Zerkleinern von Kohlen, sowie zur Herstellung, zum Kühlen und Löschen von
künstlicher Kohle.
(Schluſs des Berichtes S. 155 d. Bd.)
Mit Abbildungen auf Tafel
11.
Verfahren und Einrichtungen zum Trocknen u.s.w. von
Kohlen.
Um aus Holz, Torf, Stroh, Pflanzenmark, Baumwolle, Hanf, Flachs, Fruchtkernen,
Zuckerstärke, Gummiarten u.s.w. bei möglichst niederer Temperatur Kohle von
constanter Zusammensetzung zu erzeugen, genügen die bisher bekannten
Verkohlungsverfahren in Meilern, Kesseln oder Cylindern mit direkter Feuerung oder
überhitztem Wasserdampfe nicht oder doch nur unvollkommen. Es entfallen vielmehr
hierbei beträchtlich variirende Kohlenarten, welche auch bei Unterbrechung des
Verkohlungsprozesses noch nachkohlen, hauptsächlich in Folge der in den Kohlen
aufgespeicherten Wärme. Selbst bei geschickter Leitung des Verfahrens lassen sich in
den einzelnen Beschickungen Kohlenstoff, Sauerstoff, Wasserstoff reiche Erzeugnisse
nachweisen, wie schon die Schattirung der erzeugten Kohle, welche von roth bis
schwarz geht, anzeigt. An den Verkohlungsprozeſs schloſs sich dann das sogen.
„Dämpfen“, das oft tagelang dauerte und nie ohne qualitative und
quantitative Verluste an Kohle durchgeführt werden konnte. Man hat zur
Beschleunigung des Dämpfens zwar äuſsere Kühlung zu verwenden gesucht, aber vollen
Erfolg nicht erzielen können. Der Grund davon liegt im Wesentlichen darin, daſs bei
Ausführung dieser Operationen der Zutritt der atmosphärischen Luft zu den zu
behandelnden, glühenden oder abkühlenden frischen Kohlen nicht gehindert werden
kann, deren Porosität und Absorptionsvermögen im heiſsen frischen Zustande am
gröſsten sind. Bei dem Kühlen im Dämpfer tritt stets der Umstand ein, daſs sich nur
die Oberfläche der frisch erzeugten Kohle sättigt, während ihr Inneres seinem
Absorptionsbedürfnisse nicht genügen kann. Letzteres erwacht von Neuem bei der
Zerkleinerung und verursacht jedenfalls die Selbstentzündung des Kohlenpulvers oder
wohl gar Explosionen, wenn die Kohle zur Pulverfabrikation verwendet ist. Hermann Güttler in Reichenstein in Schlesien bewirkt daher (D. R. P. Nr. 42470 vom 12. Mai 1887) die Verkohlung selbst, sowie das Löschen
und Kühlen der fertigen Kohle im Verkohlungscylinder durch solche Gase von
entsprechender Temperatur, welche gegen den zu verkohlenden Stoff chemisch
indifferent und daher geeignet sind, dessen Verkohlung zu unterbrechen.
Es wird somit während der Verkohlung entsprechend heiſses, während der Kühlperiode
entsprechend kaltes Gas in den Verkohlungscylinder eingeführt. Hierzu geeignete Gase
sind z.B. Kohlensäure, thunlichst Sauerstoff freie Verbrennungsproducte,
Kalkofengase u.a.m.
Der zur Ausführung dieses Verfahrens dienende Ofen enthält eine Muffel M. Dieselbe trägt in ihrem Inneren den
Verkohlungscylinder C, welcher wiederum die zur
Aufnahme des zu verkohlenden Stoffes bestimmte Trommel T umschlieſst (Fig. 11). Um bequemes
Ein- und Ausbringen des Rohstoffes bezieh. der fertigen Kohle zu sichern, benutzt
man dazu zweckmäſsig eine zweite, aus T entfernbare
durchlöcherte Trommel. C sowohl wie T sind mit entsprechenden, den gegenseitigen Abstand
bestimmenden Rippen oder Bolzen versehen. Im eigentlichen Feuerraume liegt der
Ueberhitzungsapparat, hier eine Rohrschlange S (Fig. 12),
welcher durch ein Rohr r das zu erhitzende Gas
zugeführt wird. S communicirt mit C durch ein Verbindungsrohr r1. Die Destillationsproducte entweichen
mit dem zur Verkohlung benutzten Gase durch das Rohr r2. Die Rohre r1 und r2 sind entsprechend lösbar und leicht zugänglich mit
dem Deckel D2 von C verbunden, dessen andere Seite der lösbare Deckel D1 verschlieſst. C selbst und alle seine Verschlüsse müssen gasdicht
sein. Die auf dem Roste S verbrennenden Heizstoffe, in
der vorliegenden Ausführungsform Koks, erhitzen zunächst die Rohrschlange S in der Hauptsache durch Strahlung. Die Feuergase
übersteigen dann die Feuerbrücke F und erwärmen abwärts
ziehend die Muffel M von auſsen, um dann durch die
Füchse f1
f2
f3 ... nach der Esse
E zu entweichen. Der Verkohlungscylinder C ist mit Wärme- und Druckmesser versehen, um
Temperatur und Spannung dauernd controliren zu können. Nach Vollendung des
Verkohlungsprozesses werden die in den Muffelverschluſsdeckeln V1 und V2 befindlichen Löcher
l1
l2
l3... geöffnet und ein
die direkte Verbindung des Raumes zwischen M und C vermittelnder, vorher geschlossener Schieber X geöffnet, so daſs in den Raum zwischen Muffel und
Verkohlungscylinder kalte Luft zum Zwecke energischer Kühlung eingesaugt wird.
Gleichzeitig wird das Feuer vom Roste durch Ausziehen der Roststäbe entfernt und
kaltes, die Verkohlung unterbrechendes Gas durch ein die direkte Verbindung mit dem,
kaltes Gas enthaltenden Gasbehälter vermittelndes Rohr r3 dem Inneren des Verkohlungscylinders
zugeführt. Der Schieber X und die Oeffnungen l1
l2
l3 ... können auch
während des Verkohlungsprozesses zur Regelung der Temperatur benutzt werden.
Diese Ofeneinrichtung hat insofern eine Abänderung erfahren, als der
Verkohlungscylinder C in der Muffel M ausziehbar angeordnet ist und durch Einsätze in den
Verkohlungscylinder, massive oder gelochte Scheiben ab
cd (Fig.
13) oder Hülsen ef, das zum Verkohlen,
Löschen und Kühlen benutzte Gas gezwungen wird, vorgeschriebene Wege zu machen (D.
R. P. Nr. 44078 vom 29. December 1887, Zusatz zu Nr. 42470).
Eine Vorrichtung zum Zerkleinern und Sortiren von leicht zerbrechlichen Materialien
ohne Staub- und Griesbildung, in erster Linie für Steinkohle und ähnliche Stoffe
bestimmt, wird von der Maschinenbau-Anstalt „Humboldt“ in Kalk bei Köln a. Rh. hergestellt (D. R. P. Nr. 43237 vom 30. August
1887). In den Fig.
14 und 15 ist diese Maschine, welche in ihrer Anordnung etwa der unter dem Namen
„Blake'sche Steinbrecher“ bekannt
gewordenen Zerkleinerungsmaschine verglichen werden kann, dargestellt. Sie besteht
aus drei Abtheilungen B1B2B3, jede gebildet durch
die allen dreien gemeinschaftliche Brechbacke E, die
Lippen H1H2H3 und die Widerlager
J1J2J3 Zwischen H1J1 entsteht
beispielsweise eine Maulweite von 250mm, zwischen
H2J2 eine solche von
120mm und zwischen H3J3 kann das bis auf 80mm gebrachte Gut hindurchfallen. Unter H1J1, H2J2 und H3J3 sind die Siebe C1C2C3 angebracht, welche eine der darüber befindlichen
Maulweite entsprechende Lochung erhalten, also C1 eine Lochung von 120mm, C2 eine
solche von 80mm u.s.w.
Das zu bearbeitende Gut wird der Maschine schon zum Theile klassirt zugeführt, so
daſs Stücke A1 von 250
bis 600mm Raumgröſse in die Abtheilung B1 fallen und hier
unter 250mm reducirt werden, dann auf Sieb C1 gelangen, wo sie,
mit diesem Siebe direkt zugeführten Stücken A2 von weniger als 250mm Rauminhalt vereinigt, ihren Weg zwischen H2J2 hindurch suchen müssen, während die bei H1J1 bereits unter 120mm zermalmten Stücke durch dieses Sieb C1 direkt durchfallen
und auf Sieb C2
gelangen.
Die über 120mm groſsen Stücke werden zwischen H2J2 entsprechend
zerbrochen, fallen auf C2 entweder, je nach Gröſse, direkt durch dieses hindurch nach C3 oder erleiden eine
weitere Reduction zwischen H3J3 u.s.w.
Dem Siebe C2 wird
auſser dem von H2J2 und etwa auch von
C1 kommenden Gute
noch direkt klassirtes Gut A3 von entsprechender Gröſse zugeführt.
Sieb C3 ist mit
verschiedenen Maschen versehen und unten vor die Maschine hinausgeführt. Gerade
unter C2 bis unter H3J3 hat es feinste
Lochung zum Durchlasse von Staub und Gries. Weiter vorn können zwei oder mehr
Klassirungen stattfinden.
Wenn das Sieb C3 kürzer
gehalten wird, so kann das Gut auch in ein Cylindersieb L fallen, das unter der Zerkleinerungsmaschine aufgestellt ist, und in
welchem die Sortirung nach Korngröſse zwischen 80mm bis 10mm stattfindet. Die rüttelnde
Bewegung der Siebe erfolgt von irgend einer geeigneten Transmission mittels
bekannter Mechanismen. Die Brechbacke E wird von der
Achse G aus mittels Excenters in Thätigkeit gesetzt.
Der Backendrehpunkt kann auch anstatt unten (s. Zeichnung) nach oben, in die Nähe
des ersten Widerlagers gelegt werden.
Die Wirkungsweise der vorstehend beschriebenen Maschine beruht daher auf dem Prinzipe
der Arbeitstheilung, so daſs ein einmal auf eine bestimmte Gröſse gebrachtes Stück
nur dann und dort wieder einem Zerkleinerungswerkzeuge ausgesetzt wird, wann und wo
es von diesem allein reducirt werden kann, ohne Zwischentreten anderer Stücke.
Die Maschine nimmt somit nach jeder Zerkleinerung, die stufenweise erfolgt, eine Sortirung und
Klassirung des Materiales vor und führt dasselbe der seiner Gröſse entsprechenden
Abtheilung zu, ohne daſs es auf diesem Wege einer weiteren Reduction unterzogen
werden kann. Durch die so beschriebene Wirkungsart unterscheidet sich die Maschine
von allen ähnlichen Vorrichtungen.
Indessen verursacht die zermalmende oder zerquetschende Wirkung der schwingenden
Brechbacke E immer noch mehr Kleinmaterial als
wünschenswerth ist; daher ist die Maschine noch verbessert worden. Diese so
verbesserte Maschine (D. R. P. Nr. 43 903 vom 30. August 1887, Zusatz zu Nr. 43237)
ist in Fig.
16 dargestellt. An Stelle der schwingenden Brechbacke findet sich hier
eine feste Wand L mit Lippen H1H2H3 zur Bildung der Abtheilungen B1B2B3 und der enger
werdenden Oeffnungen H1J1, H2J2, H3J3. Hinter der festen
Wand L ist eine schwingende Backe F angeordnet. Dieselbe ist mit Dornen oder Stacheln D1D2D3 ausgerüstet, welche
den Widerlagern J1J2J3 gegenüber durch die
feste Wand hindurchgehen und beim Vorwärtsgange der Backe F in das zwischen L und J1J2J3 liegende Material
eindringen und es zersplittern.
Die in dieser verbesserten Form ausgeführte Maschine dürfte ohne Zweifel nach
Construction und Wirkungsweise zu den besseren neueren Zerkleinerungsmaschinen zu
zählen sein.
W. Koort.
Tafeln
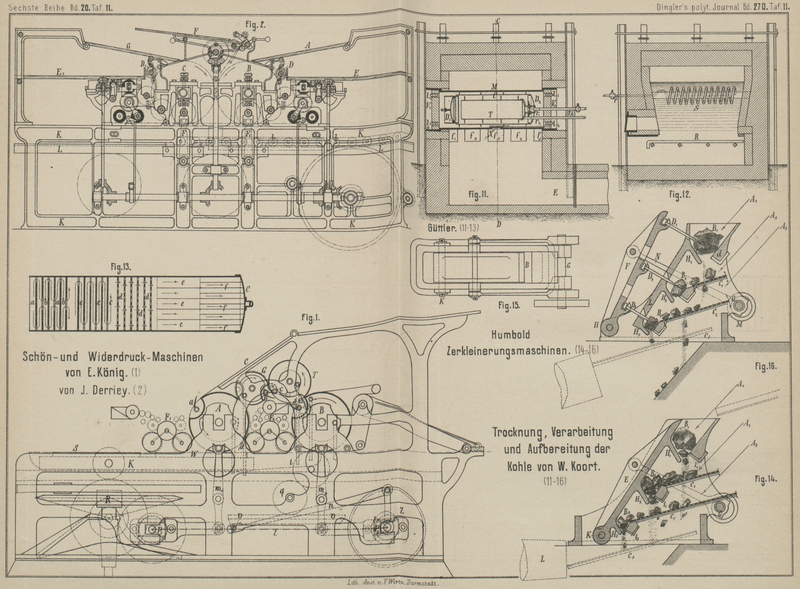